Slag-corrosion-resistant lightweight alumina clinker and preparation method thereof
A bauxite clinker and light-weight technology, which is applied in the field of slag corrosion-resistant lightweight bauxite clinker and its preparation, can solve the problems of high cost, large pore size, and large pore size of microporous lightweight bauxite refractory aggregate. Achieve the effect of improving anti-slag ability, improving material strength and low production cost
- Summary
- Abstract
- Description
- Claims
- Application Information
AI Technical Summary
Benefits of technology
Problems solved by technology
Method used
Examples
Embodiment 1
[0023] A slag corrosion-resistant lightweight alumina clinker and a preparation method thereof. The preparation method of this embodiment is:
[0024] Using 89wt% bauxite raw meal micropowder, 7wt% carbon black and 4wt% plant ash as raw materials; first mix the raw materials uniformly in a planetary ball mill, and then machine press them under 200MPa to obtain a green body; then The green body was dried at 200°C for 12 hours, and kept at 1550°C under the condition of carbon embedding for 8 hours to obtain slag corrosion-resistant lightweight bauxite clinker.
[0025] The slag corrosion-resistant lightweight bauxite clinker prepared in this example is tested: the bulk density is 2.71g / cm 3 ; The average pore diameter is 495nm; the erosion index of the anti-slag test of 1600 ℃ immersion method is 5%, and the permeability index is 15%.
Embodiment 2
[0027] A slag corrosion-resistant lightweight alumina clinker and a preparation method thereof. The preparation method of this embodiment is:
[0028] Using 90wt% bauxite raw meal powder, 9wt% carbon black and 1wt% plant ash as raw materials; firstly mix the raw materials uniformly in a planetary ball mill, and then machine press them under the condition of 160MPa to obtain a green body; then The green body was dried at 160°C for 24 hours, and kept at 1650°C under the condition of carbon embedding for 6 hours to obtain slag corrosion-resistant lightweight bauxite clinker.
[0029] The slag corrosion-resistant lightweight bauxite clinker prepared in this example is tested: the bulk density is 2.84g / cm 3 ; The average pore size is 426nm; the erosion index of the anti-slag test by immersion method at 1600°C is 5%, and the permeability index is 14%.
Embodiment 3
[0031] A slag corrosion-resistant lightweight alumina clinker and a preparation method thereof. The preparation method of this embodiment is:
[0032] Using 94wt% bauxite raw meal micropowder, 4wt% carbon black and 2wt% plant ash as raw materials; first mix the raw materials uniformly in a planetary ball mill, and then machine press them under the condition of 150MPa to obtain a green body; then The green body was dried at 150°C for 18 hours, and kept at 1600°C under the condition of carbon embedding for 5 hours to obtain slag corrosion-resistant lightweight bauxite clinker.
[0033] The slag corrosion-resistant lightweight bauxite clinker prepared in this example is tested: the bulk density is 2.94g / cm 3 ; Average pore size is 316nm; 1600 ℃ immersion method slag resistance test erosion index is 3%, permeability index is 12%.
PUM
Property | Measurement | Unit |
---|---|---|
Bulk density | aaaaa | aaaaa |
Average pore size | aaaaa | aaaaa |
Bulk density | aaaaa | aaaaa |
Abstract
Description
Claims
Application Information
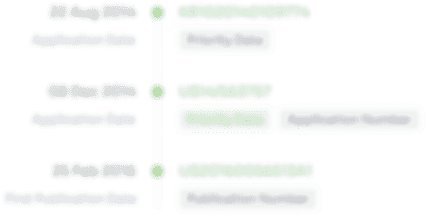
- R&D Engineer
- R&D Manager
- IP Professional
- Industry Leading Data Capabilities
- Powerful AI technology
- Patent DNA Extraction
Browse by: Latest US Patents, China's latest patents, Technical Efficacy Thesaurus, Application Domain, Technology Topic.
© 2024 PatSnap. All rights reserved.Legal|Privacy policy|Modern Slavery Act Transparency Statement|Sitemap