Pelletizing and pipe discharging integrated production equipment
A production equipment and granulation technology, which is applied in the field of integrated production equipment for granulation and pipe discharge, can solve the problems of cumbersome steps and consume a lot of time, and achieve the effect of reducing energy consumption and workload.
- Summary
- Abstract
- Description
- Claims
- Application Information
AI Technical Summary
Problems solved by technology
Method used
Image
Examples
Example Embodiment
[0020]In order to make the techniques, creative features, objective and efficacy of the present invention, and the embodiments are further illustrated in connection with the specific embodiments.
[0021]Seefigure 1 ,figure 2 versusimage 3 ,Figure 4The present invention provides a technical solution for granulation administration: the structure includes a feed groove 1, a pipe opening 2, a body 3, a base 4, a storage bin 5, an engine 6, a pumping tube 7, a pipe forming Block 8, the bottom end of the feed groove 1 is welded to the top end of the body 3, and the base 4 is integrated with the body 3, and the right end of the tube 2 is welded to the left end of the conduit shaped block 8, The pipe forming block 8 and the body 3 are integrated structures, the body 3 includes a stirring granulation mechanism 31, a housing 32, a discharge pipe 33, a block 34, a crushing mechanism 35, and the top of the agitation granulation mechanism 31 The top end in the outer casing 32 is welded, and the disch
PUM
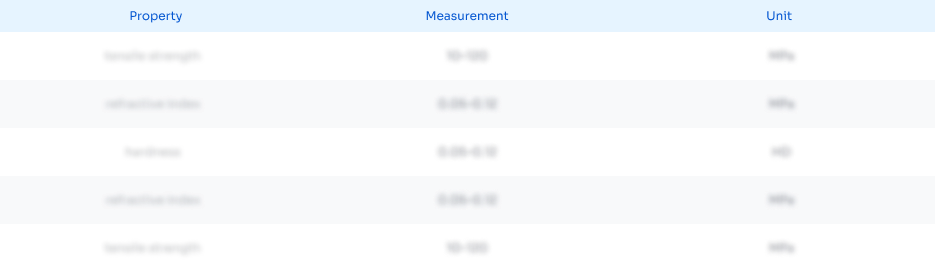
Abstract
Description
Claims
Application Information
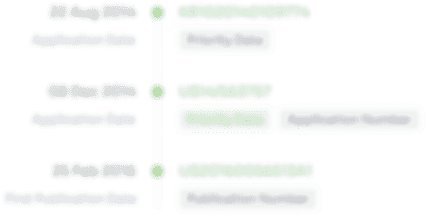
- R&D Engineer
- R&D Manager
- IP Professional
- Industry Leading Data Capabilities
- Powerful AI technology
- Patent DNA Extraction
Browse by: Latest US Patents, China's latest patents, Technical Efficacy Thesaurus, Application Domain, Technology Topic.
© 2024 PatSnap. All rights reserved.Legal|Privacy policy|Modern Slavery Act Transparency Statement|Sitemap