Process method for preparing high-silicon aluminum-silicon alloy coating through electron beams
A process method and electron beam technology, applied in the field of material surface treatment, can solve the problems of complex size and shape, micro-crack and crater structure, deterioration of the mechanical properties of the material surface, etc., to achieve the effect of improving wear resistance
- Summary
- Abstract
- Description
- Claims
- Application Information
AI Technical Summary
Problems solved by technology
Method used
Image
Examples
Embodiment 1
[0021] The weight ratio of each component of the raw material is 79.7wt.% of Al powder, 20wt.% of Si powder and 0.3wt.% of cerium oxide. A kind of process method of electron beam preparation high-silicon-aluminum-silicon alloy coating of the present invention, specifically implement according to the following steps:
[0022] (1) Powder mixing: put a part of Al powder and rare earth oxide into a powder machine for pre-mixing, the mixing time is 15s, put the pre-mixed powder and the remaining Al powder and Si powder into a stainless steel basin, and put rubber on it Hand-mix with gloves, knead until the color is uniform, sieve through 120 mesh, then put the mixture into the powder mixer, turn on the power, and the powder mixing time is 2 to 5 hours;
[0023] (2) Surface pretreatment: mix the mixed powder into cellulose ester adhesive, and apply it evenly on the polished aluminum block with a small brush to prepare for electron beam treatment;
[0024] (3) Electron beam surface mod
Embodiment 2
[0028] The difference from Example 1 is that the weight ratios of the components of the raw materials are 64.5wt.% of Al powder, 35wt.% of Si powder and 0.5wt.% of lanthanum oxide. The adhesive used in the surface pretreatment process in step (2) is polyamide.
[0029] The lanthanum oxide can be replaced by any one of cerium oxide, neodymium oxide and praseodymium oxide.
Embodiment 3
[0031] The difference from Examples 1 and 2 is that the weight ratios of the components of the raw materials are 54.2wt.% of Al powder, 45wt.% of Si powder and 0.8wt.% of neodymium oxide. The adhesive used in the surface pretreatment process in step (2) is polyvinyl acetal.
[0032] The neodymium oxide can be replaced by any one of cerium oxide, lanthanum oxide and praseodymium oxide.
[0033] Performance test: MG-2000 high-speed high-temperature friction and wear testing machine is used to conduct friction and wear tests on the samples treated with electron beams to investigate the wear resistance of the samples. The total number of revolutions of each sample on the friction pair is 2000 revolutions. The rotation speed is controlled at 250 rpm, the total sliding distance is 0.38km, the sliding speed is 0.8m / s, and the applied load is 10N. Use the amount of wear to measure the wear resistance of the sample, that is, the sample is ultrasonically cleaned with acetone before and
PUM
Property | Measurement | Unit |
---|---|---|
L | aaaaa | aaaaa |
Abstract
Description
Claims
Application Information
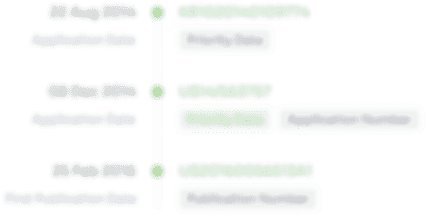
- R&D Engineer
- R&D Manager
- IP Professional
- Industry Leading Data Capabilities
- Powerful AI technology
- Patent DNA Extraction
Browse by: Latest US Patents, China's latest patents, Technical Efficacy Thesaurus, Application Domain, Technology Topic.
© 2024 PatSnap. All rights reserved.Legal|Privacy policy|Modern Slavery Act Transparency Statement|Sitemap