Continuous production process of hardware assembly
一种生产工艺、组件的技术,应用在五金组件的连续式生产工艺领域,能够解决无法工件防锈处理等问题,达到同步运动效果好、安装孔位置准确、垂直度好的效果
- Summary
- Abstract
- Description
- Claims
- Application Information
AI Technical Summary
Problems solved by technology
Method used
Examples
Embodiment 1
[0046] like Figures 1 to 5 As shown, a continuous production process of hardware components is characterized in that it comprises the following steps:
[0047] Step 1, base plate pretreatment, the base plate 20 is pre-machined to open splicing grooves and installation holes, and then placed on the base plate feeding group 5 one by one for transportation;
[0048] Step 2, the pretreatment of the vertical board, the vertical board 10 is drilled and cut by machining in advance, and then stacked and placed on the operating platform 11 of the vertical board feeding group 1;
[0049]Step 3, the disassembly and assembly process, the disassembly unit 13 laterally separates the two stacked vertical panels 10 into a group, and then the push unit 12 synchronously pushes the two vertical panels 10 forward, and the two vertical panels 10 are respectively received by the receiving parts a23 and the receiving part b24 take over, and when the dismantling unit 13 laterally separates the vert...
Embodiment 2
[0060] like figure 2 , 3 , 4, 5 and 16, a metal base tailor welding anti-rust integrated machine for mechanical equipment, including a feeding mechanism and a slotting mechanism 3, is characterized in that it also includes:
[0061] Flatten body 2;
[0062] finished product gripping device 7; and
[0063] Finished product conveyor line 8;
[0064] The feeding mechanism provides a riser 10 and a bottom plate 20 to the splicing mechanism 2, and the splicing mechanism 2 splices and welds two risers 10 and a bottom plate 20 into a whole;
[0065] The finished product grasping device 7 grasps the welded finished product for antirust work, and then transmits it to the finished product conveying line 8 for output.
[0066] Further, the feeding mechanism includes:
[0067] Riser Feed Group 1; and
[0068] Bottom plate feeding group 5;
[0069] The vertical plate feeding group 1 includes a propulsion unit 12 and a dismantling unit 13, the propelling unit 12 pushes two vertical ...
PUM
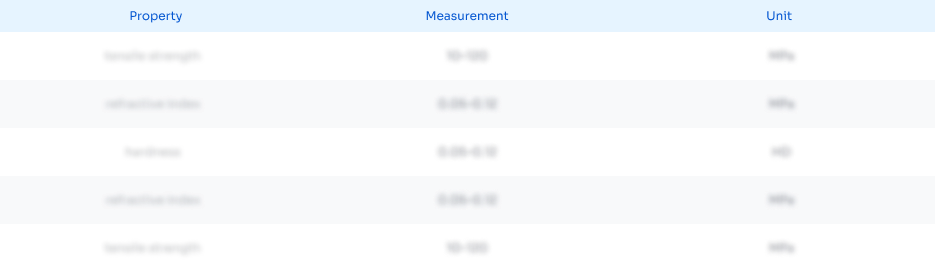
Abstract
Description
Claims
Application Information
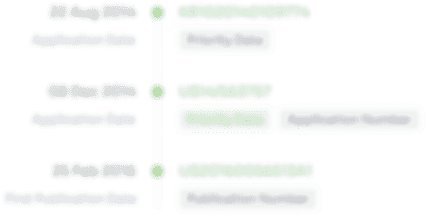
- R&D Engineer
- R&D Manager
- IP Professional
- Industry Leading Data Capabilities
- Powerful AI technology
- Patent DNA Extraction
Browse by: Latest US Patents, China's latest patents, Technical Efficacy Thesaurus, Application Domain, Technology Topic.
© 2024 PatSnap. All rights reserved.Legal|Privacy policy|Modern Slavery Act Transparency Statement|Sitemap