Preparation method of modified intumescent flame-retardant cellulose fibers
A technology of flame-retardant cellulose and expansion type, which is applied in the field of flame-retardant cellulose fiber and its preparation, can solve the problems of difficult realization and complicated process, and achieve the effect of simple operation and less addition
- Summary
- Abstract
- Description
- Claims
- Application Information
AI Technical Summary
Benefits of technology
Problems solved by technology
Method used
Examples
Embodiment 1
[0030] 1. Preparation of intumescent flame retardant system
[0031] Weigh TEOS, organic solvent, and oil bath solution with a mass ratio of 1:6:20 in a container, stir at room temperature for 30 minutes, add a certain amount of acetic acid to adjust the pH to 4, and add ammonium polyphosphate twice the mass of TEOS The temperature of the solution was raised to 70° C. and the stirring was continued for 30 minutes to obtain an intumescent flame retardant system containing modified ammonium polyphosphate, ammonium polyphosphate and TEOS.
[0032] The organic solvent is ethanol, and the oil concentration in the oil bath is 10g / L;
[0033] The ammonium polyphosphate is type I ammonium polyphosphate with a degree of polymerization of 50.
[0034] 2. Preparation of flame retardant viscose fiber
[0035] Add the unoiled fiber in the refining section to the above system, the bath ratio is 1:20, continue to stir for 60 minutes, press and adjust the drying process: bake at 100°C for 2
Embodiment 2
[0039] 1. Establishment of intumescent flame retardant system
[0040] Weigh TEOS, organic solvent, and oil bath in a mass ratio of 1:2:10 in a container, stir at room temperature for 10 minutes, and add a certain amount of acetic acid to adjust the pH to 5. After adding ammonium polyphosphate of the same quality as TEOS, the temperature of the solution was raised to 40°C and continued stirring for 10 minutes to obtain an intumescent flame retardant system containing modified ammonium polyphosphate, ammonium polyphosphate and TEOS.
[0041] The organic solvent used in the process is ethanol and n-butanol with a mass ratio of 1:1, and the concentration of oil agent in the oil bath is 8g / L;
[0042] The ammonium polyphosphate is type I ammonium polyphosphate with a degree of polymerization of 50.
[0043] 2. Preparation of flame retardant viscose fiber
[0044] Add the unoiled fiber in the refining section to the above system, continue to stir for 30 minutes at a liquor ratio o
Embodiment 3
[0048] 1. Establishment of intumescent flame retardant system
[0049] Weigh TEOS, organic solvent, and oil bath solution with a mass ratio of 1:3:15 in a container, stir at room temperature for 20 minutes, and add a certain amount of acetic acid to adjust the pH to 4. After adding ammonium polyphosphate 1.5 times the mass of TEOS, the temperature of the solution was raised to 60°C and continued to stir for 20 minutes to obtain an intumescent flame retardant system containing modified ammonium polyphosphate, ammonium polyphosphate and TEOS.
[0050] The organic solvent used in this process is ethanol, n-butanol and isobutanol with a mass ratio of 1:1:1, and the concentration of oil agent in the oil bath is 6g / L;
[0051] The ammonium polyphosphate is type I ammonium polyphosphate with a degree of polymerization of 50.
[0052] 2. Preparation of flame retardant viscose fiber
[0053] Add the unoiled fiber in the refining section to the above system, continue to stir for 20 minut
PUM
Property | Measurement | Unit |
---|---|---|
Dry breaking strength | aaaaa | aaaaa |
Breaking strength | aaaaa | aaaaa |
Dry breaking strength | aaaaa | aaaaa |
Abstract
Description
Claims
Application Information
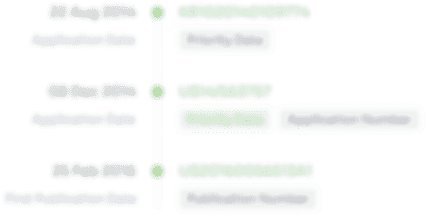
- R&D Engineer
- R&D Manager
- IP Professional
- Industry Leading Data Capabilities
- Powerful AI technology
- Patent DNA Extraction
Browse by: Latest US Patents, China's latest patents, Technical Efficacy Thesaurus, Application Domain, Technology Topic.
© 2024 PatSnap. All rights reserved.Legal|Privacy policy|Modern Slavery Act Transparency Statement|Sitemap