Preparation process of improved sulfur-resistant sintering flue gas decarburization catalyst
A technology for sintering flue gas and preparation process, applied in physical/chemical process catalysts, chemical instruments and methods, chemical/physical processes, etc., can solve problems such as poisoning, limited application, catalyst deactivation, etc. number, and the effect of improving the catalytic oxidation performance of low-temperature CO.
- Summary
- Abstract
- Description
- Claims
- Application Information
AI Technical Summary
Benefits of technology
Problems solved by technology
Method used
Image
Examples
Embodiment 1
[0023] The invention is an improved sulfur-resistant sintered flue gas decarburization catalyst, which is modified by phosphorylation of transition metal oxides rich in oxygen vacancies, and uses nano-sized anatase TiO 2 Prepared by carrying out loading, and then performing calcination treatment in an inert atmosphere;
Embodiment 2
[0025] A method for preparing an improved sulfur-resistant sintered flue gas decarburization catalyst, comprising the following steps:
[0026] Step 1: Add copper sulfate, phosphoric acid and deionized water to the reactor, heat and stir for reaction, stop stirring after the reaction is over; add titanium dioxide after cooling, continue heating and stirring; obtain the first reactant;
[0027] Among them, the mass ratio of copper sulfate, phosphoric acid and titanium dioxide is 1:1.0:8; the reaction temperature of copper sulfate and phosphoric acid is 38°C, and the reaction time is 3 hours; the stirring temperature after adding titanium dioxide is 38°C, and the stirring time is 3 hours;
[0028] Step 2: Raise the temperature of the first reactant, remove the solvent and evaporate the solution to dryness, dry the residue and place it in a tube furnace, pass in an inert gas for calcination, and cool down to room temperature; obtain an improved sulfur-resistant sintering flue gas de
Embodiment 3
[0033] A method for preparing an improved sulfur-resistant sintered flue gas decarburization catalyst, comprising the following steps:
[0034] Step 1: Add copper sulfate, phosphoric acid and deionized water to the reactor, heat and stir for reaction, stop stirring after the reaction is over; add titanium dioxide after cooling, continue heating and stirring; obtain the first reactant;
[0035] Among them, the mass ratio of copper sulfate, phosphoric acid and titanium dioxide is 1:1.5:9; the reaction temperature of copper sulfate and phosphoric acid is 40°C, and the reaction time is 4 hours; the stirring temperature after adding titanium dioxide is 40°C, and the stirring time is 4 hours;
[0036] Step 2: Raise the temperature of the first reactant, remove the solvent and evaporate the solution to dryness, dry the residue and place it in a tube furnace, pass in an inert gas for calcination, and cool down to room temperature; obtain an improved sulfur-resistant sintering flue gas de
PUM
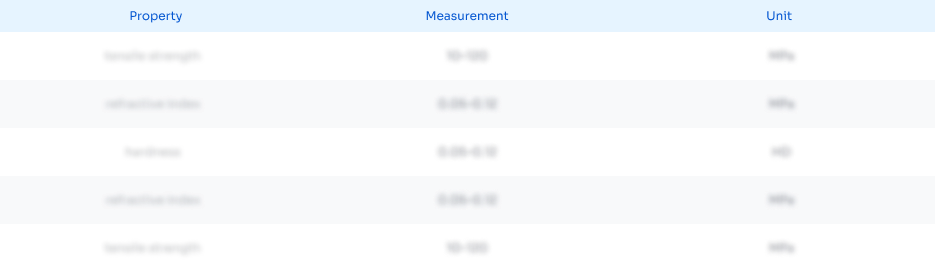
Abstract
Description
Claims
Application Information
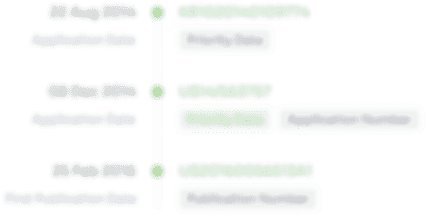
- R&D Engineer
- R&D Manager
- IP Professional
- Industry Leading Data Capabilities
- Powerful AI technology
- Patent DNA Extraction
Browse by: Latest US Patents, China's latest patents, Technical Efficacy Thesaurus, Application Domain, Technology Topic.
© 2024 PatSnap. All rights reserved.Legal|Privacy policy|Modern Slavery Act Transparency Statement|Sitemap