Honeycomb plate metal strip edge sealing extrusion forming device
A sheet metal extrusion molding technology, which is applied in the field of honeycomb sheet metal edge banding extrusion molding device, can solve the problems of low production efficiency of metal edge banding, difficult continuous feeding of metal edge banding, and cumbersome process of metal edge banding and other issues to achieve the effect of improving production efficiency, convenient observation, and convenient organization
- Summary
- Abstract
- Description
- Claims
- Application Information
AI Technical Summary
Benefits of technology
Problems solved by technology
Method used
Image
Examples
Embodiment Construction
[0034] In order to make the technical means realized by the present invention, creative features, goals and effects easy to understand, the following combination Figure 1 to Figure 9 , to further elaborate the present invention.
[0035] refer to figure 1 and figure 2 , a honeycomb plate metal strip edge-sealing extrusion molding device, including a workbench 1, a feeding device 2, an extrusion device 3, a forming device 4 and a collection frame 5, and the upper right side of the workbench 1 is equipped with a feeding device 2. An extruding device 3 is installed in the middle of the upper end of the workbench 1. The right end of the extruding device 3 is slidingly arranged on the lower side of the feeding device 2, and the right end of the extruding device 3 is installed with a forming device 4, which is installed on the feeding device 2. lower end.
[0036] refer to Figure 4 , the upper side of the right end of the workbench 1 is provided with a blanking hole, the collect
PUM
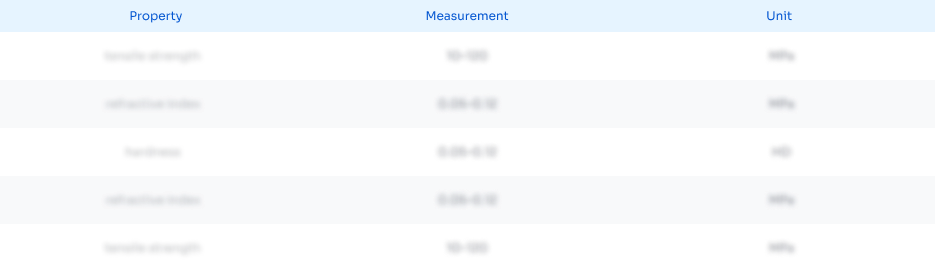
Abstract
Description
Claims
Application Information
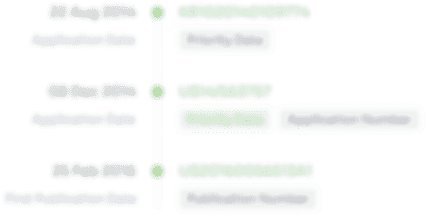
- R&D Engineer
- R&D Manager
- IP Professional
- Industry Leading Data Capabilities
- Powerful AI technology
- Patent DNA Extraction
Browse by: Latest US Patents, China's latest patents, Technical Efficacy Thesaurus, Application Domain, Technology Topic.
© 2024 PatSnap. All rights reserved.Legal|Privacy policy|Modern Slavery Act Transparency Statement|Sitemap