Antibacterial high-strength glass and preparation method thereof
A high-strength, high-strength glass technology, applied in glass production and other directions, can solve the problems of difficult product quality assurance, poor scratch resistance of the film layer, and high technical difficulty, and achieve good resistance, good light transmittance, and simple process Effect
- Summary
- Abstract
- Description
- Claims
- Application Information
AI Technical Summary
Benefits of technology
Problems solved by technology
Method used
Examples
Embodiment 1
[0024] Preparation method of antibacterial high-strength glass, comprising the following steps:
[0025] (1) Clean the soda-lime glass substrate, remove oil and dust, and then put it into the oven to dry, the drying temperature is 60 ° C, and the drying time is 30 minutes;
[0026] (2) Potassium nitrate is heated and melted, and heated to 430 °C to obtain potassium nitrate molten salt;
[0027] (3) In order to avoid glass bursting, the glass substrate will be preheated in advance and then quickly and completely immersed in potassium nitrate molten salt for ion exchange, the exchange time is 6 hours, and the temperature is maintained at 430 °C;
[0028] (4) Take out the glass substrate after the exchange is completed and cool, then clean it and put it into the drying oven to dry, the drying temperature is 60 ° C, and the drying time is 30 minutes;
[0029] (5) The mixture of potassium nitrate and silver nitrate is 98% potassium nitrate by weight, and 2% of silver nitrate is mixed and
Embodiment 2
[0033] Preparation method of antibacterial high-strength glass, comprising the following steps:
[0034] (1) Clean the aluminosilicate glass substrate, remove oil and dust, and then put it into the oven to dry at a temperature of 60 ° C, and the drying time is 30 minutes;
[0035] (2) Potassium nitrate is heated and melted, and heated to 450 ° C to obtain potassium nitrate molten salt;
[0036](3) In order to avoid glass bursting, the glass substrate will be preheated in advance and then quickly and completely immersed in potassium nitrate molten salt for ion exchange, the exchange time is 8 hours, and the temperature is maintained at 450 °C;
[0037] (4) Take out the glass substrate after the exchange is completed and cool, then clean it and put it into the drying oven to dry, the drying temperature is 60 ° C, and the drying time is 30 minutes;
[0038] (5) The mixture of potassium nitrate and silver nitrate is 99% of potassium nitrate by weight, and 1% of silver nitrate is mixed an
Embodiment 3
[0042] (1) Clean the borosilicate glass substrate, remove oil and dust, and then put it into the oven to dry at a temperature of 60 ° C, and the drying time is 30 minutes;
[0043] (2) Potassium nitrate is heated and melted, and heated to 480 ° C to obtain potassium nitrate molten salt;
[0044] (3) In order to avoid glass bursting, the glass substrate will be preheated in advance and then quickly and completely immersed in potassium nitrate molten salt for ion exchange, the exchange time is 10 hours, and the temperature is maintained at 480 °C;
[0045] (4) Take out the glass substrate after the exchange is completed and cool, then clean it and put it into the drying oven to dry, the drying temperature is 60 ° C, and the drying time is 30 minutes;
[0046] (5) The mixture of potassium nitrate and silver nitrate is 99.99% potassium nitrate by weight, and silver 0.01% nitrate is mixed and melted, and heated to 450 °C to obtain a mixed molten salt;
[0047] (6) In order to avoid glass
PUM
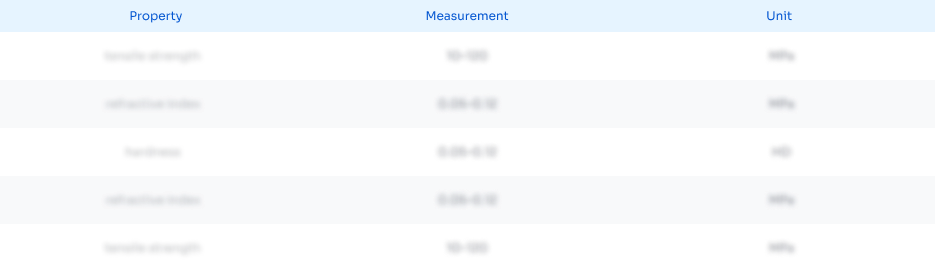
Abstract
Description
Claims
Application Information
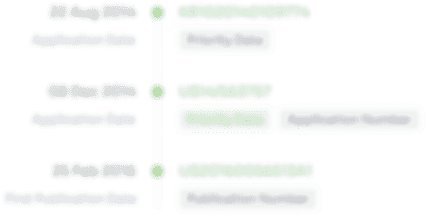
- R&D Engineer
- R&D Manager
- IP Professional
- Industry Leading Data Capabilities
- Powerful AI technology
- Patent DNA Extraction
Browse by: Latest US Patents, China's latest patents, Technical Efficacy Thesaurus, Application Domain, Technology Topic.
© 2024 PatSnap. All rights reserved.Legal|Privacy policy|Modern Slavery Act Transparency Statement|Sitemap