Method and device for continuously producing ultra-pure arsine
An arsine and ultra-pure technology, applied in chemical instruments and methods, arsenic compounds, inorganic chemistry, etc., can solve the problems of uncontinuous production of arsine products, unstable product quality, low production efficiency, etc., to achieve large output, The effect of mild reaction and low risk
- Summary
- Abstract
- Description
- Claims
- Application Information
AI Technical Summary
Problems solved by technology
Method used
Image
Examples
Embodiment example 1
[0061] After the nitrogen replacement system was evacuated, 540Kg of deionized water was added to the first reactor A and the second reactor B in turn, and the stirring was turned on. Concentrated sulfuric acid, control the temperature of the first reaction kettle A and the second reaction kettle B not to exceed 40 ° C, then gradually add 180Kg of zinc arsenide, the sulfuric acid and zinc arsenide react with exothermic heat, control the rate of addition of zinc arsenide, and maintain the temperature of the reaction solution 40°C, rotating speed 120r / min, maintaining system pressure of 0.2MPa and producing crude arsine gas. No gas was generated after the reaction for 5 hours, the reaction was completed, and the reaction solution was discharged. When the reaction liquid is discharged, a small amount of the reaction liquid is left to act as a liquid seal to prevent the discharge of arsine gas. The first reactor A and the second reactor B are alternately fed in parallel to produce
Embodiment example 2
[0065] After the nitrogen replacement system was evacuated, 360Kg of deionized water was added to the first reactor A and the second reactor B in turn, and the stirring was turned on. Sulfuric acid, control the temperature of the first reaction kettle A and the second reaction kettle B not to exceed 70 ℃, then gradually add 180Kg of zinc arsenide, the sulfuric acid and the zinc arsenide react with exothermic heat, control the rate of addition of the zinc arsenide, and keep the temperature of the reaction solution at 70 °C ℃, the rotation speed is 90r / min, the system pressure is maintained at 0.2MPa, and the crude arsine gas is produced. After the reaction for 3.5 hours, no gas was produced, the reaction was completed, and the reaction solution was discharged. When the reaction liquid is discharged, a small amount of the reaction liquid is left to act as a liquid seal to prevent the discharge of arsine gas. The first reactor A and the second reactor B are alternately fed in par
Embodiment example 3
[0069] After the nitrogen replacement system was evacuated, 400Kg of deionized water was added to the first reactor A and the second reactor B in turn, and the stirring was turned on. Sulfuric acid, control the temperature of the first reaction kettle A and the second reaction kettle B not to exceed 65 ℃, then gradually add 180Kg of zinc arsenide, the sulfuric acid and the zinc arsenide react with exothermic heat, control the rate of addition of the zinc arsenide, and keep the temperature of the reaction solution at 65 ℃, the rotation speed is 100r / min, the system pressure is maintained at 0.1MPa, and the crude arsine gas is produced. No gas was generated after the reaction for 4 hours, the reaction was completed, and the reaction solution was discharged. When the reaction liquid is discharged, a small amount of the reaction liquid is left to act as a liquid seal to prevent the discharge of arsine gas. The first reactor A and the second reactor B are alternately fed in paralle
PUM
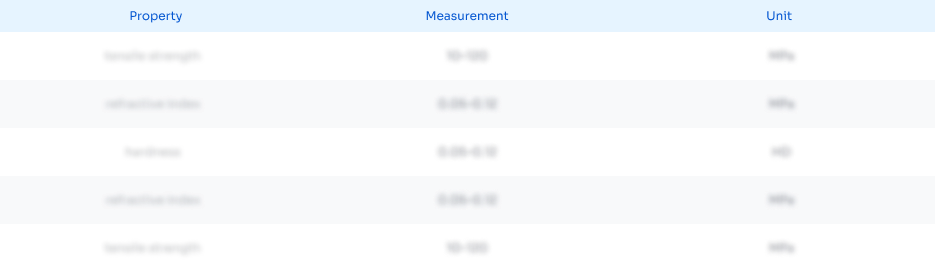
Abstract
Description
Claims
Application Information
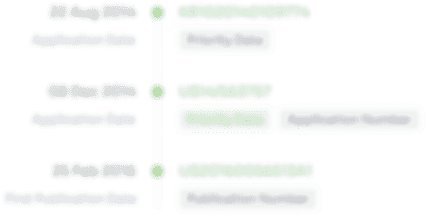
- R&D Engineer
- R&D Manager
- IP Professional
- Industry Leading Data Capabilities
- Powerful AI technology
- Patent DNA Extraction
Browse by: Latest US Patents, China's latest patents, Technical Efficacy Thesaurus, Application Domain, Technology Topic.
© 2024 PatSnap. All rights reserved.Legal|Privacy policy|Modern Slavery Act Transparency Statement|Sitemap