Velocit cracking method
A technology of hydrocarbon oil and cracking conditions, applied in cracking, catalytic cracking, petroleum industry, etc., can solve the problems of poor anti-wear performance, insufficient increase of gasoline octane number, difficult implementation, etc., and achieves easy implementation and good performance The effect of anti-wear properties
- Summary
- Abstract
- Description
- Claims
- Application Information
AI Technical Summary
Benefits of technology
Problems solved by technology
Method used
Examples
preparation example Construction
[0019] The preparation method of the catalyst comprises drying the slurry containing molecular sieve, binder precursor and deionized water, containing or not containing clay, calcined or not calcined, wherein the molecular sieve has a fluorine content of 0.01-5% by weight The molecular sieve is used in such a way that the final catalyst contains, based on the total amount of the catalyst, 10-70% by weight of fluorine-containing molecular sieve, 10-60% by weight of binder and 0-75% by weight of clay.
[0020] Wherein, based on the fluorine-containing molecular sieve, the fluorine content in the fluorine-containing molecular sieve is preferably 0.1-3% by weight. The preparation method of the fluorine-containing molecular sieve includes mixing the fluoride aqueous solution with the molecular sieve, or impregnating the molecular sieve with the fluoride aqueous solution, filtering or not filtering, and then drying. Wherein, the fluoride is selected from one or more of water-soluble fl
example 1
[0030] This example illustrates the catalyst used in the method provided by the invention and its preparation method.
[0031] (1) 10 kilograms of HY zeolite (unit cell constant is 24.57 angstroms, Na 2 The O content is 0.5% by weight (produced by Zhoucun Catalyst Factory), mixed uniformly with 15 liters of hydrogen fluoride aqueous solution with a concentration of 0.5 mol / liter, filtered, and the filter cake was dried at 110°C to obtain fluorine-containing HY zeolite with 0.63% by weight of fluorine . The fluorine content was determined by X-ray fluorescence spectrometry.
[0032] (2) Combine the fluorine-containing HY zeolite obtained in (1) with silica-alumina sol (SiO 2 The content is 65% by weight, Al 2 o 3 Content is 15% by weight (produced by Zhoucun Catalyst Factory), mixed at a dry basis weight ratio of 60:40, then deionized water is added, beating and mixed to make a slurry with a solid content of 25% by weight. The resulting slurry was spray-dried at a temperatu
example 2
[0035] This example illustrates the catalyst used in the method provided by the invention and its preparation method.
[0036] The catalyst was prepared according to the method of Example 1, except that the silica-alumina sol was replaced by pseudo-boehmite (solid content: 61% by weight, produced by Shandong Aluminum Factory) to obtain catalyst C2. The composition and attrition index of catalyst C2 are listed in Table 1.
PUM
Property | Measurement | Unit |
---|---|---|
Cell constant | aaaaa | aaaaa |
Cell constant | aaaaa | aaaaa |
Abstract
Description
Claims
Application Information
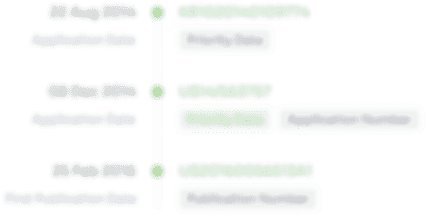
- R&D Engineer
- R&D Manager
- IP Professional
- Industry Leading Data Capabilities
- Powerful AI technology
- Patent DNA Extraction
Browse by: Latest US Patents, China's latest patents, Technical Efficacy Thesaurus, Application Domain, Technology Topic.
© 2024 PatSnap. All rights reserved.Legal|Privacy policy|Modern Slavery Act Transparency Statement|Sitemap