High bath-strength polypropylene and method for preparing same
A technology of high melt strength and polypropylene, applied in the field of composite materials, can solve the problems of high cost and complicated process, and achieve the effects of good modulus, low preparation cost and simple preparation method
- Summary
- Abstract
- Description
- Claims
- Application Information
AI Technical Summary
Benefits of technology
Problems solved by technology
Method used
Examples
Embodiment 1
[0015] The composition and weight percentage of the high melt strength polypropylene are: polypropylene: 60%, compatibilizer maleic anhydride grafted polypropylene: 30%, clay organically modified montmorillonite: 10%.
[0016] Weigh 600g of polypropylene, 300g of maleic anhydride grafted polypropylene and 100g of organically modified montmorillonite, stir in a high-speed mixer for 15 minutes to mix evenly, and then use a twin-screw extruder to knead the premix at 170°C , extruded, granulated, and molded into standard splines for performance testing. The performance is shown in Table 1.
Embodiment 2
[0018] The composition and weight percentage of the high melt strength polypropylene are: polypropylene: 96%, compatibilizer (maleic anhydride grafted polypropylene): 3%, clay (organically modified montmorillonite): 1%.
[0019] Weigh 960g of polypropylene, 30g of maleic anhydride grafted polypropylene and 10g of organically modified montmorillonite, stir in a high-speed mixer for 20 minutes to mix evenly, and then use an internal mixer to mix and crush the premix at 190°C , molded into standard splines, and performed performance tests. The properties are shown in Table 1.
Embodiment 3
[0021] The composition and weight percentage of the high melt strength polypropylene are: polypropylene: 72%, compatibilizer (maleic anhydride grafted polypropylene): 21%, clay (organically modified montmorillonite): 7%.
[0022] Weigh 720g of polypropylene, 210g of maleic anhydride grafted polypropylene and 70g of organically modified montmorillonite, stir in a high-speed mixer for 10 minutes to mix evenly, and then use an internal mixer to mix and crush the premix at 210°C , molded into standard splines, and performed performance tests. The properties are shown in Table 1.
PUM
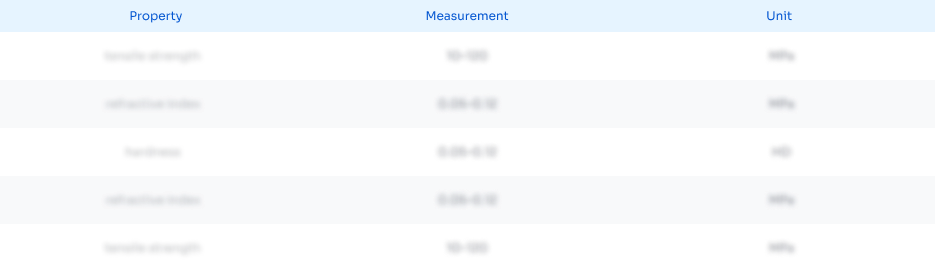
Abstract
Description
Claims
Application Information
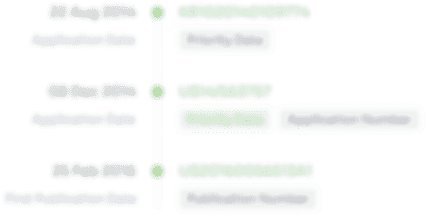
- R&D Engineer
- R&D Manager
- IP Professional
- Industry Leading Data Capabilities
- Powerful AI technology
- Patent DNA Extraction
Browse by: Latest US Patents, China's latest patents, Technical Efficacy Thesaurus, Application Domain, Technology Topic.
© 2024 PatSnap. All rights reserved.Legal|Privacy policy|Modern Slavery Act Transparency Statement|Sitemap