Connecting rod assembly for an internal combustion engine and method of manufacturing same
a technology of connecting rods and internal combustion engines, which is applied in the direction of connecting rod bearings, manufacturing tools, machines/engines, etc., can solve the problems of engine failure, excess material along the small end of the connecting rod assembly, and impose an additional step in the manufacturing process that is costly and labor-intensive, so as to reduce the width configuration, reduce the moment force, and streamline manufacturing
- Summary
- Abstract
- Description
- Claims
- Application Information
AI Technical Summary
Benefits of technology
Problems solved by technology
Method used
Image
Examples
Embodiment Construction
[0031] A connecting rod assembly manufactured pursuant to the method of the present invention is generally indicated at 10 throughout the figures, where like numbers are used to designate like structures throughout the drawings. As shown in FIG. 1, the present invention is particularly adapted for use in an internal combustion engine, generally indicated at 12. In this case, the assembly 10 of the present invention is illustrated in connection with a single cylinder 14 of an internal combustion engine 12 having a dual-overhead cam arrangement. Those having ordinary skill in the art will appreciate that the engine 12 is but one of the many internal combustion engines with which the present invention may be employed. By way of example, the present invention may be employed to manufacture a connecting rod assembly used in a two-stroke or four-stroke engine. The cylinders may be arranged in an in-line, v-shaped, or flat manner or in any other manner commonly known in the art. The present i
PUM
Property | Measurement | Unit |
---|---|---|
Temperature | aaaaa | aaaaa |
Diameter | aaaaa | aaaaa |
Width | aaaaa | aaaaa |
Abstract
Description
Claims
Application Information
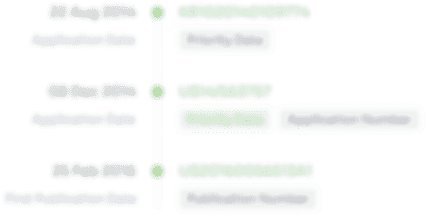
- R&D Engineer
- R&D Manager
- IP Professional
- Industry Leading Data Capabilities
- Powerful AI technology
- Patent DNA Extraction
Browse by: Latest US Patents, China's latest patents, Technical Efficacy Thesaurus, Application Domain, Technology Topic.
© 2024 PatSnap. All rights reserved.Legal|Privacy policy|Modern Slavery Act Transparency Statement|Sitemap