Negative-acting photolithographic printing plate with improved pre-burn performance
a negative-acting, photolithographic printing technology, applied in the direction of lithography, photosensitive materials, instruments, etc., can solve the problems of insufficient pre-burn performance of negative working printing form precursors, inability to achieve one or more desirable features of the prior art, and the natural sensitivity of diazonium salt compositions to near infra-red or infra-red laser irradiation. to achieve the effect of increasing the plate performan
- Summary
- Abstract
- Description
- Claims
- Application Information
AI Technical Summary
Benefits of technology
Problems solved by technology
Method used
Image
Examples
example 2
[0069]A solution in Dowanol™ solvent PM (Dow Chemical Wilmington, Del.) and MEK consisting of 2 g of the acetal resin 1 0.02 g of CYMEL™ 303 (American Cyanamid Co., Wayne, N.J.), 0.02 g TTT, (2,4,6-tris(trichloromethyl)-1,3,5-triazine PCAS, France), 0.0072 g malachite green (Aldrich Chemicals, Milwaukee, Wis.) and 0.003 g of 2,2-bis(hydroxymethyl)-2,3-dihydro-1H-perimidine based squarylium dye made according to U.S. Pat. No. RE 38,251 1d was coated with a No. 6 coating rod (R&D Specialties, Webster, N.Y.) onto 200 micron-thick grained and anodized aluminum printing plate base and dried in an oven at 90° C. for 3 minutes.
example 3
[0070]A solution in Dowanol™ solvent PM (Dow Chemical Wilmington, Del.) and MEK consisting of 2 g of the acetal resin 2 0.02 g of CYMEL™ 303 (American Cyanamid Co., Wayne, N.J.), 0.02 g TTT, (2,4,6-tris(trichloromethyl)-1,3,5-triazine PCAS, France), 0.0072 g malachite green (Aldrich Chemicals, Milwaukee, Wis.) and 0.003 g of 2,2-bis(hydroxymethyl)-2,3-dihydro-1H-perimidine based squarylium dye made according to U.S. Pat. No. RE 38,251 1d was coated with a No. 6 coating rod (R&D Specialties, Webster, N.Y.) onto 200 micron-thick grained and anodized aluminum printing plate base and dried in an oven at 90° C. for 3 minutes.
[0071]The plates thus prepared of comparative example 1, example 2 and example 3 were imaged on a Newsetter® 70 made by Creo, Inc. using 15 W. Plates were subsequently pre-heated at a range of temperatures and developed in 830N developer (Southern Lithoplate Inc., Youngsville, N.C.) for 30s, the exposed areas remained and the unexposed areas were washed off to leave a n
example 4
[0072]A solution in Dowanol™ solvent PM (Dow Chemical Wilmington, Del.) and MEK consisting of 2 g of the acetal resin 1 0.02 g of CYMEL 303 (American Cyanamid Co., Wayne, N.J.), 0.02 g TTT, (2,4,6-tris(trichloromethyl)-1,3,5-triazine PCAS, France), 0.0072 g crystal violet (Aldrich Chemicals, Milwaukee, Wis.). 0.003 g of 2,2-bis(hydroxymethyl)-2,3-dihydro-1H-perimidine based squarylium dye made according to U.S. Pat. No. RE 38,251 1d and 0.001 g surfactant FC430 (Minnesota Mining and Manufacturing Co), was coated with a No. 6 coating rod (R&D Specialties, Webster, N.Y.) onto 200 micron-thick grained and anodized aluminum printing plate base and dried in an oven at 90° C. for 3 minutes. The plates of comparative example 1, example 2 and example 3 were imaged on a Newsetter™ 70 made by Creo, Inc. using 15 W. Plates were subsequently pre-heated at a range of temperatures and developed in 830N developer Southern Lithoplate, Youngsville, N.C.) for 30 seconds (s), the exposed areas remained a
PUM
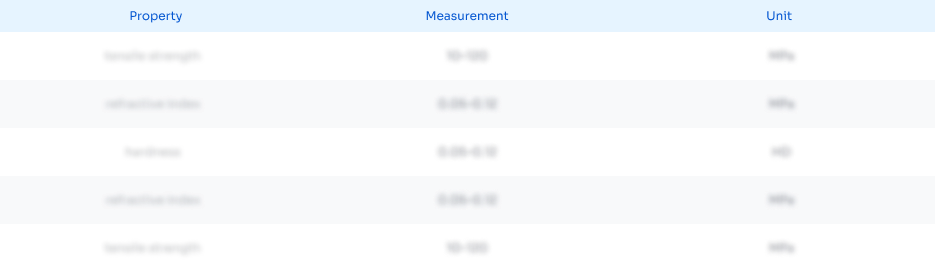
Abstract
Description
Claims
Application Information
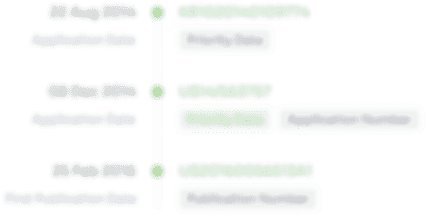
- R&D Engineer
- R&D Manager
- IP Professional
- Industry Leading Data Capabilities
- Powerful AI technology
- Patent DNA Extraction
Browse by: Latest US Patents, China's latest patents, Technical Efficacy Thesaurus, Application Domain, Technology Topic.
© 2024 PatSnap. All rights reserved.Legal|Privacy policy|Modern Slavery Act Transparency Statement|Sitemap