Laminated plate and end treatment method of the laminated plate
a technology of laminated plates and end treatments, which is applied in the direction of hollow wall objects, soldering devices, auxillary welding devices, etc., can solve the problems of large wrinkles on a portion, deterioration of the appearance of an and the bent portion concerned has not been brought into good contact with the side end portion of the laminated pla
- Summary
- Abstract
- Description
- Claims
- Application Information
AI Technical Summary
Benefits of technology
Problems solved by technology
Method used
Examples
Embodiment Construction
[0022]A description will be made below in detail of an embodiment of the present invention while referring to the drawings. Here, a floorboard laid in a trunk room of an automobile is illustrated as a laminated plate.
[0023]FIG. 1 is a perspective view showing a laminated material according to this embodiment, onto which a nonwoven fabric is pasted, FIG. 2 is an exploded perspective view showing a structure of the laminated material onto which the nonwoven fabric is pasted, FIG. 3 is a cross-sectional view of the laminated material onto which the nonwoven fabric is pasted, FIG. 4 is an exploded perspective view showing a state where the laminated material onto which the nonwoven fabric is pasted is mounted on a heating apparatus, FIG. 5 is a cross-sectional view showing the state where the laminated material onto which the nonwoven fabric is pasted is mounted on the heating apparatus, FIG. 6 is an exploded perspective view showing a state where the laminated material onto which the n...
PUM
Property | Measurement | Unit |
---|---|---|
degree of freedom | aaaaa | aaaaa |
non-air-permeable | aaaaa | aaaaa |
time | aaaaa | aaaaa |
Abstract
Description
Claims
Application Information
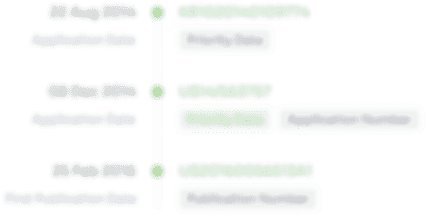
- R&D Engineer
- R&D Manager
- IP Professional
- Industry Leading Data Capabilities
- Powerful AI technology
- Patent DNA Extraction
Browse by: Latest US Patents, China's latest patents, Technical Efficacy Thesaurus, Application Domain, Technology Topic.
© 2024 PatSnap. All rights reserved.Legal|Privacy policy|Modern Slavery Act Transparency Statement|Sitemap