Methods for automated application of hardfacing material to drill bits
- Summary
- Abstract
- Description
- Claims
- Application Information
AI Technical Summary
Benefits of technology
Problems solved by technology
Method used
Image
Examples
Embodiment Construction
[0065]The system and method of the present invention have an opposite configuration and method of operation to that of manual hardfacing and prior automated hardfacing systems. In the present system and method a robotic system is used, having a plasma transfer arc torch secured in a substantially vertical position to a torch positioner in a downward orientation. The torch positioner is program-controllable in a vertical plane. Shielding, plasma, and transport gases are supplied to the torch through electrically controllable flow valves. Rather than use a torch positioner, a robotic arm can be used having a transfer arc torch secured thereto in a substantially vertical position in a downward orientation. For handling a roller cone, a robot having program controllable movement of an articulated arm is used. A chuck adapter is attached to the arm of the robot. A three jaw chuck is attached to the chuck adapter. The chuck is capable of securely holding a roller cone in an inverted position
PUM
Property | Measurement | Unit |
---|---|---|
Time | aaaaa | aaaaa |
Length | aaaaa | aaaaa |
Length | aaaaa | aaaaa |
Abstract
Description
Claims
Application Information
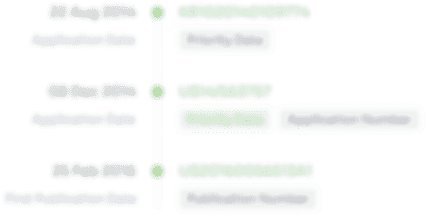
- R&D Engineer
- R&D Manager
- IP Professional
- Industry Leading Data Capabilities
- Powerful AI technology
- Patent DNA Extraction
Browse by: Latest US Patents, China's latest patents, Technical Efficacy Thesaurus, Application Domain, Technology Topic.
© 2024 PatSnap. All rights reserved.Legal|Privacy policy|Modern Slavery Act Transparency Statement|Sitemap