Photocurable fluorinated copolymer composition
a fluorinated copolymer and composition technology, applied in the field of photocurable fluorinated copolymer composition, can solve the problems of poor photosensitivity, substantial shrinkage at the curing time, and poor photocation polymerization of epoxy groups, etc., to achieve excellent heat resistance and abrasion resistance, excellent weather resistance performance, and excellent transparency
- Summary
- Abstract
- Description
- Claims
- Application Information
AI Technical Summary
Benefits of technology
Problems solved by technology
Method used
Image
Examples
production example 1
Production of Fluorinated Copolymer (A-1))
[0191]Into a stainless steel autoclave having an internal capacity of 300 ml and equipped with a stirrer, 3-ethyl-3-vinyloxymethyloxetane (22.4 g) to form the units (a-2), hydroxybutyl vinyl ether (9.1 g) to form the units (a-3), cyclohexyl vinyl ether (19.8 g) to form the units (a-4), xylene (95.0 g), ethanol (17.7 g) and potassium carbonate (1.0 g) were introduced all at once, and dissolved oxygen was removed by nitrogen.
[0192]Then, chlorotrifluoroethylene (45.8 g) to form the units (a-1) was introduced into the autoclave, the temperature was gradually raised, and when it reached 55° C., a xylene solution (0.6 g) containing 50% of t-butyl peroxypivalate was introduced into the autoclave over a period of two hours, followed by further stirring for 15 hours, whereupon the reaction was terminated. After the reaction, potassium carbonate was removed by filtration, and ethanol and a part of xylene were distilled off by evaporation so that a non-vo
production example 2
Production of Fluorinated Copolymer (A-2))
[0195]Into a stainless steel autoclave having an internal capacity of 300 ml and equipped with a stirrer, 3-ethyl-3-vinyloxymethyloxetane (33.6 g) to form the units (a-2), hydroxybutyl vinyl ether (9.1 g) to form the units (a-3), cyclohexyl vinyl ether (9.9 g) to form the units (a-4), xylene (95.0 g), ethanol (17.7 g) and potassium carbonate (1.0 g) were introduced all at once, and dissolved oxygen was removed by nitrogen.
[0196]Then, chlorotrifluoroethylene (45.8 g) to form the units (a-1) was introduced into the autoclave, the temperature was gradually raised, and after it reached 55° C., a xylene solution (0.6 g) containing 50% of t-butyl peroxypivalate was introduced into the autoclave over a period of two hours, followed by further stirring for 15 hours, whereupon the reaction was terminated. After the reaction, potassium carbonate was removed by filtration, and ethanol and a part of xylene were distilled off by evaporation so that a non-vo
production example 3
Production of Fluorinated Copolymer (A-3))
[0199]The fluorinated copolymer (A-2) (200.0 g) obtained in Production Example 2 was transferred to a four-necked flask having a capacity of 500 ml and equipped with a thermometer, a reflux condenser and a stirrer, and 3-isocyanate propyltriethoxysilane (27.6 g), xylene (33.5 g) and tin 2-ethylhexanoate (0.04 g) were added, followed by a reaction at 50° C. for 5 hours in a nitrogen atmosphere.
[0200]The infrared absorption spectrum of the obtained solution was measured, whereby no absorption peak was observed in the absorption band of an isocyanate group, and instead, a large absorption peak was observed in the absorption band of an urethane bond. Thus, formation of the fluorinated copolymer (A-3) having alkoxysilyl groups was confirmed.
[0201]After the reaction, trimethyl orthoformate (8.6 g) and isopropanol (8.6 g) were added, and adjustment was made so that a non-volatile component of the fluorinated copolymer (A-3) would be 60%.
[0202]From H1-
PUM
Property | Measurement | Unit |
---|---|---|
Percent by mass | aaaaa | aaaaa |
Percent by mass | aaaaa | aaaaa |
Percent by mass | aaaaa | aaaaa |
Abstract
Description
Claims
Application Information
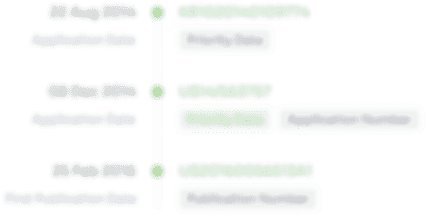
- R&D Engineer
- R&D Manager
- IP Professional
- Industry Leading Data Capabilities
- Powerful AI technology
- Patent DNA Extraction
Browse by: Latest US Patents, China's latest patents, Technical Efficacy Thesaurus, Application Domain, Technology Topic.
© 2024 PatSnap. All rights reserved.Legal|Privacy policy|Modern Slavery Act Transparency Statement|Sitemap