Anti-sublimation silica gel printing coating and preparation method thereof
A technology of silica gel and printing, applied in dyeing, textile and papermaking, etc., can solve the problems of unfavorable printing color effectively, insufficient transparency, dark color, etc., achieve uniform and effective adsorption, increase adsorption effect, and good transparency.
- Summary
- Abstract
- Description
- Claims
- Application Information
AI Technical Summary
Problems solved by technology
Method used
Examples
preparation example Construction
[0035] The preparation method includes the following steps:
[0036] Step 1, prepare anti-lifting base silica gel: Ethylene polysiloxane, orthosilicate and n-heptane are prepared in a mixture of 500-1000 rpm rotational speeds of 15-30 min, and mix evenly, add deionized water. The mixture was continued for 5-10 min to give a mixed solution, and the mixed solution was placed in a pressure-resistant hydrothermal reaction kettle, and the reaction was reacted at 120-150 ° C for 8-10 h to obtain a lifted base silicone;
[0037] Step 2, prepare a component: Add white carbon black and platinum catalyst to the anti-lifting base silica gel, uniformly dispersed by the planetary mixer, and remove the residual n-heptane and deionized water at a temperature of from 100 to 10 ° C. A component;
[0038] Step 3: Preparation of B components: Silicone oil and inhibitors are uniformly dispersed in a mixer of 500-1000 rpm to 5-10 min to obtain B components;
[0039] Step 4: Preparation of anti-lifting...
Embodiment 1
[0044] This example uses a method of preventing subtilizing silica gel printing coatings, which is prepared for the preparation of anti-lifting silicone printing coatings;
[0045] The preparation method includes the following steps:
[0046] Step 1: Preparation of anti-lifting base silica gel: 100 parts of the two-terminal vinyl polymethylsiloxane, 5 parts of n-silicate and 10 parts of n-heptane are uniformly dispersed in a mixer of 500 rpm rotational speeds 30 min, and mix Uniform, then 0.05 parts of deionized water, continued for 10 min to obtain a mixed solution, and the mixed solution was placed in a pressure-resistant hydrothermal reaction kettle, and the reaction was reacted at 120 ° C for 8 h, resulting in anti-lifting base silica gel; wherein said The viscosity of the double-end vinyl polymethylsiloxane is 1000 mPa · s, and the vinyl content is 0.2%;
[0047] Step 2, prepare a component: 10 parts of the surface-treated gas phase method white charcoal black and 0.9 parts of ...
Embodiment 2
[0052] This example uses a method of preventing subtilizing silica gel printing coatings, which is prepared for the preparation of anti-lifting silicone printing coatings;
[0053] The preparation method includes the following steps:
[0054] Step 1: Preparation of anti-lifting base silica gel: 100 parts of the two-end polyimethylsiloxane, 15 parts of n-silicate and 15 n-heptane in the mixer of 500 rpm rotational speed 30 min, both mix Uniform, then 0.08 parts of deionized water, continued for 5 min to give a mixed solution, and the mixed solution was placed in a pressure-resistant hydrothermal reaction kettle, and the reaction was reacted at 120 ° C for 8 h, resulting in anti-lifting base silica gel; wherein said The viscosity of double-end vinyl polymethylsiloxane is 2000 MPa · S, and the vinyl content is 0.18%;
[0055] Step 2, prepare a component: add 5 partially treated gas phases to the anti-lifting base silica gel and 0.9 parts of H. 2 PTC l6 The isopropyl alcohol solution ...
PUM
Property | Measurement | Unit |
---|---|---|
Viscosity | aaaaa | aaaaa |
Viscosity | aaaaa | aaaaa |
Thickness | aaaaa | aaaaa |
Abstract
Description
Claims
Application Information
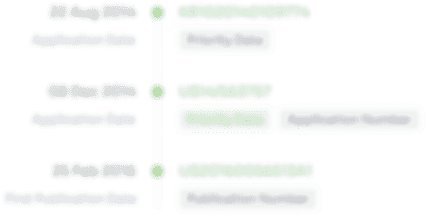
- R&D Engineer
- R&D Manager
- IP Professional
- Industry Leading Data Capabilities
- Powerful AI technology
- Patent DNA Extraction
Browse by: Latest US Patents, China's latest patents, Technical Efficacy Thesaurus, Application Domain, Technology Topic.
© 2024 PatSnap. All rights reserved.Legal|Privacy policy|Modern Slavery Act Transparency Statement|Sitemap