Manufacture of a filtration membrane
- Summary
- Abstract
- Description
- Claims
- Application Information
AI Technical Summary
Benefits of technology
Problems solved by technology
Method used
Image
Examples
example 1
Membranes based on Polyethersulfone (PES)
[0057]A spin assembly as shown in FIG. 1 can be used for the production of conventional filtration membranes by extrusion. Such an assembly comprises a tank of collodion 1 and a tank of internal liquid 2, both connected to an extrusion spinneret 3 that allows forming a nascent fiber. This nascent fiber falls into a precipitation bath 4 and, by means of take-up rollers 4b is, is guided toward a rinsing bay 5 and a bundling machine 6 which is used to roll it. For experimental spinning, the bundling machine 6 is not used and the nascent fiber falls directly into a basin of water extending to the exit from the large roller of the rinsing bay 5, which advances it forward.
[0058]To manufacture conventional membranes based on polyethersulphone (PES), collodion can be prepared from a polymer mixture containing 16% Veradel 3100P polyethersulfone in the presence of 6% polyvinylpyrrolidone K30 in N-methylpyrrolidone, while stirring and at a temperature main
example 2
Membranes Based on Polyacrylonitrile (PAN)
[0085]To manufacture conventional membranes based on polyacrylonitrile (PAN), a polymer (collodion) mixture is prepared containing 18% polyacrylonitrile in the presence of 2% lithium chloride in N-methylpyrrolidone, while stirring at a temperature maintained at 70° C.
[0086]The collodion is then filtered through a wire mesh (5 micron filtration rating) and transferred to a storage tank where it is vacuum-degassed and then stored at a temperature of 40° C.
[0087]The precipitation liquid is water, degassed by ultrasound and then stored prior to use in a tank maintained at 40° C.
[0088]The hollow fiber is produced with the collodion and internal fluid at a temperature of 40° C. A specific extrusion spinneret is used to produce a fiber having an inner diameter of 0.90 mm and an outer diameter of 1.62 mm.
[0089]The spinning speed used is 18 m / min.
[0090]The external rinsing bath is filled with water maintained at 40° C. The fiber exiting the bath is ad
example 3
Filtration Modules
[0108]The table below gives the filtration areas that can be provided by a filtration module manufactured according to the invention, having an inner diameter of 300 mm and an effective filtration length equal to 1,200 mm. Three configurations of membranes of the invention are considered:
[0109]1—A membrane 15 as illustrated in FIG. 6, having a single series of thirty-three channels 16 (Series 1) placed between two layers of support film 17 measuring 1.5 mm in total thickness, which is a bonding area of 1.5×40 mm. This membrane is suitable for all potential cut-offs, from microfiltration to nanofiltration.
[0110]2—A membrane 15 as illustrated in FIG. 7, having two series of thirty channels 16 (Series 2) placed between two layers of support film 17 measuring 2.7 mm in total thickness, which is a bonding area equal to 2.7×40 mm. This membrane is more suitable for high ultrafiltration, ultrafiltration, or nanofiltration applications.
[0111]3—A membrane 15 as illustrated in
PUM
Property | Measurement | Unit |
---|---|---|
Temperature | aaaaa | aaaaa |
Temperature | aaaaa | aaaaa |
Force | aaaaa | aaaaa |
Abstract
Description
Claims
Application Information
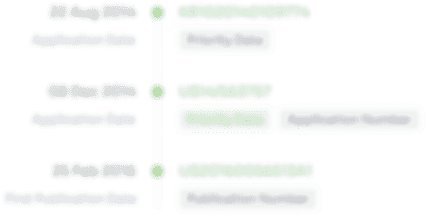
- R&D Engineer
- R&D Manager
- IP Professional
- Industry Leading Data Capabilities
- Powerful AI technology
- Patent DNA Extraction
Browse by: Latest US Patents, China's latest patents, Technical Efficacy Thesaurus, Application Domain, Technology Topic.
© 2024 PatSnap. All rights reserved.Legal|Privacy policy|Modern Slavery Act Transparency Statement|Sitemap