Gas separation membrane module with integrated filter
a technology of gas separation membrane and filter, which is applied in the direction of membranes, separation processes, dispersed particle separation, etc., can solve the problems of occupying valuable space, difficult to regenerate the beds, and reducing the process efficiency, so as to reduce the space requirements of the gas separation membrane system and eliminate the need for a carbon bed
- Summary
- Abstract
- Description
- Claims
- Application Information
AI Technical Summary
Benefits of technology
Problems solved by technology
Method used
Image
Examples
example
[0054]A commercial air separation module was fitted with a custom pad of Zorflex FM50K, having a six-ply thickness, and having dimensions of 1.125×0.12 inches. The Zorflex material is sold in sheets of 0.5 mm thickness. The pad was attached to the feed end cap of the module.
[0055]The module was operated for three weeks, with a compressed air feed stream having a pressure of 120 psig. The feed stream contained about 0.1-0.5 ppm oil vapor, and the flow rate of the feed stream was 50 scfh, to produce a calculated residence time, in the filter, of 0.045 seconds.
[0056]A second module, without the filter pad, but otherwise the same as the first module, was run with the same feed air stream.
[0057]A third module, similar to the others, was operated with a standard carbon bed, positioned upstream of the module, in which the residence time of the feed stream, in the filter, was one second.
[0058]Both before and after the above-described three-week treatment, the modules were tested at standard co
PUM
Property | Measurement | Unit |
---|---|---|
Time | aaaaa | aaaaa |
Pressure | aaaaa | aaaaa |
Abstract
Description
Claims
Application Information
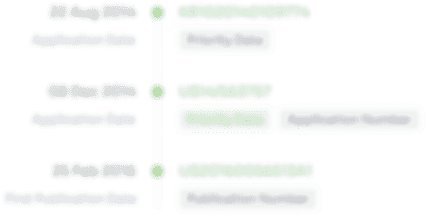
- R&D Engineer
- R&D Manager
- IP Professional
- Industry Leading Data Capabilities
- Powerful AI technology
- Patent DNA Extraction
Browse by: Latest US Patents, China's latest patents, Technical Efficacy Thesaurus, Application Domain, Technology Topic.
© 2024 PatSnap. All rights reserved.Legal|Privacy policy|Modern Slavery Act Transparency Statement|Sitemap