Elastic member
- Summary
- Abstract
- Description
- Claims
- Application Information
AI Technical Summary
Benefits of technology
Problems solved by technology
Method used
Image
Examples
examples
[0052]The invention is illustrated more fully below by way of Working Examples and Comparative Examples, although the invention is not limited by these Examples.
working examples 1 to 4
, Comparative Examples 1 to 5
[0053]The polyurethane composition formulated as shown below was stirred in an Cakes mixer while feeding 113 cc / min of air per 100 cc / min of polyol. The reaction mixture was then sheeted onto a film with a bar coater and dried at 150° C. for 15 minutes, giving a 2 mm×500 mm×500 mm polyurethane foam sheet. This was used as the base.
[Polyurethane Composition]
[0054]
Polyol 1100parts by weight(Sannix GS-3000, from Sanyo ChemicalIndustries, Ltd.)Polyol 25parts by weight(1,4-butanediol, from BASF)Isocyanate (isocyanate index, 105)30parts by weight(Sumidur 44V20, from Sumika Bayer UrethaneKK)Tin catalyst0.02part by weightSilicone foam stabilizer4parts by weight(NIAX SILICONE L626, from MomentivePerformance Materials Japan)
[0055]In a separate procedure, water-based coatings formulated as shown in Table 1 were prepared. Each of the resulting water-based coatings was applied by spraying onto one surface of the sheet-like base made of polyurethane foam and dried to
working examples 5 to 7
, Comparative Examples 6 to 8
[0062]Water-based coatings in which the content of the low-friction powder (Tospearl 145) was changed as shown in Table 2 from the formulation in Working Example 1 were prepared, and elastic members having a resin coating layer on the surface were produced in the same way as in Working Example 1. The 100% modulus, film formability and coefficient of dynamic friction for the resulting resin coating layers and elastic members were measured or evaluated in the same way as in Working Example 1. The results are shown in Table 2, which also presents the results for Working Example 1.
TABLE 2Comp.ComparativeEx.Working ExampleExample6561778FormulationWater-based80808080808080(pbw)coating A(resin content,35 wt %)Water-based20202020202020coating B(resin content,35 wt %)Low-viscosity00.62615.717.535powder*(1.71)(5.71)(17.14)(44.86)(50)(100)Co-solvent6666666(butyl cellosolve)Diluent (water)88888888888888Film100% modulus (MPa)27.627.627.627.627.627.610propertiesProductFi
PUM
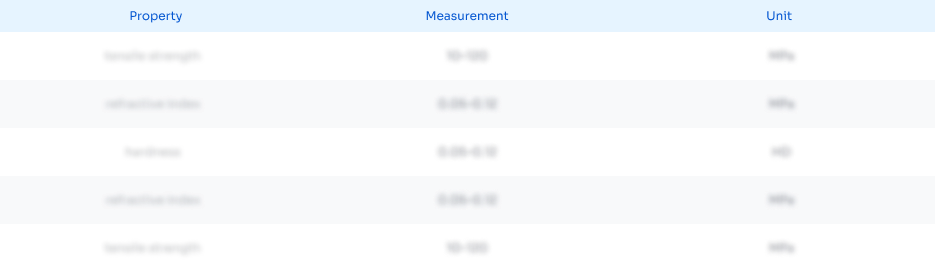
Abstract
Description
Claims
Application Information
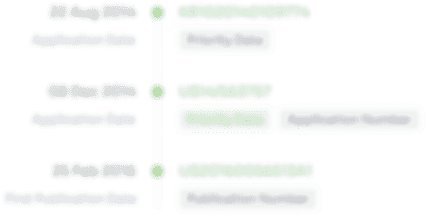
- R&D Engineer
- R&D Manager
- IP Professional
- Industry Leading Data Capabilities
- Powerful AI technology
- Patent DNA Extraction
Browse by: Latest US Patents, China's latest patents, Technical Efficacy Thesaurus, Application Domain, Technology Topic.
© 2024 PatSnap. All rights reserved.Legal|Privacy policy|Modern Slavery Act Transparency Statement|Sitemap