Endless belt and method of manufacturing the endless belt
- Summary
- Abstract
- Description
- Claims
- Application Information
AI Technical Summary
Benefits of technology
Problems solved by technology
Method used
Image
Examples
example 2
[0078] An endless belt according to Example 2 of the present invention was obtained in a manner similar to that as in Example 1, except that a tetrafluoroethylene-perfluoroalkoxyethylene copolymer (product of DuPont Company: "540CL") having, as an additive, 2.5 wt % of conductive carbon was used here for the release layer. No wrinkles were observed on the thus obtained endless belt.
example 3
[0079] A molding die was prepared, which was formed of a pipe made of stainless steel (SUS304) having an inner diameter of 60 mm, a thickness of 3 mm and a mirror-polished outer circumferential surface. On the outer circumferential surface of the molding die, a polytetrafluoroethylene (product of Daikin Industries, Ltd.: "ED-4839BD") provided with electrical conductivity was coated to a thickness of 35 .mu.m as a release layer, and thereafter was baked at 380.degree. C. for 15 minutes. After the baking, the thickness of the release layer was 20 .mu.m.
[0080] Next, the molding die was cooled to room temperature, and thereafter the surface of the release layer was subjected to etching treatment using a fluororesin treatment agent "Tetra-Etch".
[0081] Subsequently, on the release layer, a silicone rubber (product of Shinetsu Silicone Co., Ltd.: "KE-1241"), as an elastic layer, was coated and was baked at 250.degree. C. for 30 minutes. After the baking, the elastic layer had a thickness of 2
example 4
[0083] An endless belt according to Example 4 of the present invention was obtained in a manner similar to that as in Example 1, except that here the support layer (thickness of 80 .mu.m) formed of the polyimide varnish (product of I.S.T Corporation: "RC-5057") was made to contain a filler made of a heat generating material. For the heat generating material, silver flakes having an average particle size of 9 .mu.m was used. The mixing ration of the polyimide varnish to the silver flakes was: polyimide varnish / silver flakes =1 / 2 in terms of volume ratio. No wrinkles were observed on the surface of the thus obtained endless belt.
PUM
Property | Measurement | Unit |
---|---|---|
Temperature | aaaaa | aaaaa |
Elasticity | aaaaa | aaaaa |
Heat | aaaaa | aaaaa |
Abstract
Description
Claims
Application Information
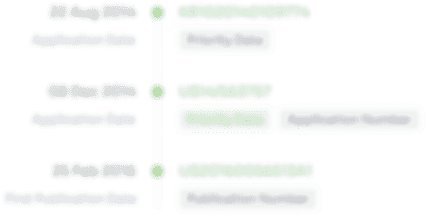
- R&D Engineer
- R&D Manager
- IP Professional
- Industry Leading Data Capabilities
- Powerful AI technology
- Patent DNA Extraction
Browse by: Latest US Patents, China's latest patents, Technical Efficacy Thesaurus, Application Domain, Technology Topic.
© 2024 PatSnap. All rights reserved.Legal|Privacy policy|Modern Slavery Act Transparency Statement|Sitemap