Multilayer breathable films and laminates including the same
a technology of breathable films and laminates, applied in the field of multi-layer breathable films, can solve the problems of composite products that are not naturally hygroscopic, composite products that are not providing a consistent balance of high breathability, and often experience a decrease in adhesion between monolithic films, etc., and achieves a high level of breathability and high water absorption rate
- Summary
- Abstract
- Description
- Claims
- Application Information
AI Technical Summary
Benefits of technology
Problems solved by technology
Method used
Image
Examples
example 3
[0093]The raw materials used in this example are two polyether-block-esters, namely Arnitel® A and Arnitel® B, both from DSM under the brand name of Arnitel®. The Arnitel® A resin has a melting temperature of 189° C., volume melt flow rate of 46 cm3 / 10 min when tested per ISO 1133 and a water absorption rate of 0.7% per ISO 62. The Arnitel® B resin has a melting temperature of 185° C., volume melt flow rate of 10 cm3 / 10 min when tested per ISO 1133 and a water absorption rate of 35% per ISO 62. They were dried at 85° C. for at least 4 hours in a dehumidifying drier and then co-extruded to a 3.5 meter wide cast film die, where the die was equipped with a combining block and the temperature was set at 220° C.±2° C. The ‘A’ layers are a blend of Arnitel® A and an anti-block process agent. The ‘B’ layer was 100% Arnitel® B. By controlling the melt temperature, melt pressure, extrusion rate, chill roll speed and other parameters, a 12 gsm film (Sample B) with above structure (i.e., ABA)
example 4
[0094]Each of the above films were laminated with two layers of nonwovens, where the film is sandwiched between the nonwoven layers with a hot melt adhesive. The first nonwoven was a typical polypropylene spunbond, which can be made from a formulation that comprises mainly isotactic polypropylene having a viscosity of 35±5 MFR. The second nonwoven was a typical polypropylene spunbond, which can be made from a formulation that comprises mainly isotactic polypropylene having a viscosity of 35±5 MFR for spunbond grade resins and a viscosity ranged from 300-2000 MFR for melt blown grade resins as measured by ISO 1133 (230° C. and 2.16 Kg). Such nonwovens can be made on Reicofil spunmelt production equipment sold by Reifenhauser Reicofil, Troisdorf, Germany. The structures of these laminates and their typical properties are presented in Table 2.
TABLE 2Laminate Examples and Their Key PropertiesViralBasisCDTrapHydroBarrierSampleFilmweightGrabTearhead,MVTRByIDusedgsmlbflbfmbarg / sm / dayF1671
example 5
[0095]Heat seals forming seams of samples E and F were conducted using a pilot heat seal machine, model PW3024 from Packworld USA. In general, these materials can be properly sealed at a sealing temperature ranged from 190-220° C., a sealing pressure 3-4 PSI per inch of seal bar, and a sealing time of 3-6 second when using the heat seal machine. The seams are identified as ‘EE’ and ‘FF’, respectively, and evaluated by seam tensile strength, hydro head pressure, and F1671 test. The seam tensile strength was tested following ASTM D5035-95 with the seam being oriented perpendicular to the pulling force direction. The hydro head pressure test was a modified hydro head test according to AATCC 127 to simulate the pressuring step of F1671. During the hydro head pressure test, a supportive screen (34 gsm PET spunbond, Reemay®, Style No. 2014) was used above the heat seal seam specimen. The pressure was increased to 140 mbar, and this pressure was held steady for 60 seconds. A seam is considere
PUM
Property | Measurement | Unit |
---|---|---|
Temperature | aaaaa | aaaaa |
Percent by mass | aaaaa | aaaaa |
Thickness | aaaaa | aaaaa |
Abstract
Description
Claims
Application Information
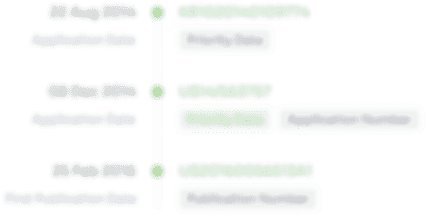
- R&D Engineer
- R&D Manager
- IP Professional
- Industry Leading Data Capabilities
- Powerful AI technology
- Patent DNA Extraction
Browse by: Latest US Patents, China's latest patents, Technical Efficacy Thesaurus, Application Domain, Technology Topic.
© 2024 PatSnap. All rights reserved.Legal|Privacy policy|Modern Slavery Act Transparency Statement|Sitemap