Polymer modified bentonite and preparation process thereof
A bentonite and polymer technology, applied in the field of polymer modified bentonite and its preparation, can solve problems such as poor hydration performance, limited water absorption capacity of bentonite, poor chemical compatibility, etc., to achieve increased viscosity, improved chemical compatibility, improved The effect of layer spacing
- Summary
- Abstract
- Description
- Claims
- Application Information
AI Technical Summary
Problems solved by technology
Method used
Examples
Embodiment 1
[0023] The polymer modified bentonite preparation process of the present embodiment is specifically as follows:
[0024] Step 1. Weigh 40 parts of bentonite and 4 parts of magnesia for mixing. The mixing ratio of bentonite and magnesia is 10:1. After mixing evenly, grind the mixture until the particle size is 200-250 mesh ;
[0025] Step 2. Put 2 parts of acrylic acid, 15 parts of N,N-dimethylbisacrylamide, and 2 parts of lye in a nitrogen atmosphere to react for 5 to 7 hours until the flocculation state is formed, and then dry , dried and prepared into flake resin for later use;
[0026] Step 3, preparing polyurethane polymer: 27 parts of water-based polyurethane emulsion, 9 parts of isocyanate, and 9 parts of polyol are mixed, mixed into a high-temperature emulsion, and subjected to vacuum distillation to obtain polyurethane polymer;
[0027] Step 4: Stir 7 parts of the lubricant, the flake resin in step 2, and the polyurethane polymer in step 3, heat up to 70±5°C, treat a...
Embodiment 2
[0029] The polymer modified bentonite preparation process of the present embodiment is specifically as follows:
[0030] Step 1. Weigh 40 parts of bentonite and 4 parts of magnesia for mixing. The mixing ratio of bentonite and magnesia is 10:1. After mixing evenly, grind the mixture until the particle size is 200-250 mesh ;
[0031] Step 2. Put 1 part of acrylic acid, 10 parts of N,N-dimethylbisacrylamide, and 1 part of lye in a nitrogen atmosphere to react for 5-7 hours until the flocculation state is formed, and then dry , dried and prepared into flake resin for later use;
[0032] Step 3, preparing polyurethane polymer: mixing 20 parts of water-based polyurethane emulsion, 5 parts of isocyanate, and 5 parts of polyol, mixing into a high-temperature emulsion, and distilling under reduced pressure to obtain polyurethane polymer;
[0033] Step 4: Stir 5 parts of the lubricant, the flake resin in step 2, and the polyurethane polymer in step 3, heat up to 70±5°C, treat at a co...
Embodiment 3
[0035] The polymer modified bentonite preparation process of the present embodiment is specifically as follows:
[0036] Step 1. Weigh 60 parts of bentonite and 6 parts of magnesia for mixing. The mixing ratio of bentonite and magnesia is 10:1. After mixing evenly, grind the mixture until the particle size is 200-250 mesh ;
[0037] Step 2. Put 3 parts of acrylic acid, 16 parts of N,N-dimethylbisacrylamide, and 2 parts of lye in a nitrogen atmosphere to react for 5 to 7 hours until the flocculation state is formed, and then dry , dried and prepared into flake resin for later use;
[0038] Step 3, preparing polyurethane polymer: mixing 30 parts of water-based polyurethane emulsion, 10 parts of isocyanate, and 10 parts of polyol, mixing into a high-temperature emulsion, and distilling under reduced pressure to obtain polyurethane polymer;
[0039] Step 4: Stir 9 parts of the lubricant, the flake resin in step 2, and the polyurethane polymer in step 3, heat up to 70±5°C, treat ...
PUM
Property | Measurement | Unit |
---|---|---|
particle diameter | aaaaa | aaaaa |
Abstract
Description
Claims
Application Information
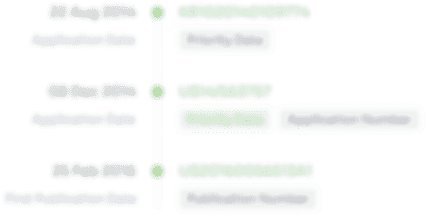
- R&D Engineer
- R&D Manager
- IP Professional
- Industry Leading Data Capabilities
- Powerful AI technology
- Patent DNA Extraction
Browse by: Latest US Patents, China's latest patents, Technical Efficacy Thesaurus, Application Domain, Technology Topic.
© 2024 PatSnap. All rights reserved.Legal|Privacy policy|Modern Slavery Act Transparency Statement|Sitemap