Optical non-uniformity compensation (NUC) for passive imaging sensors using micro-electro-mechanical system (MEMS) micro-mirror arrays (MMAS)
a technology of optical non-uniformity compensation and imaging sensor, which is applied in the field of non-uniformity compensation (nuc) for passive imaging sensors, can solve the problems of fixed pattern noise, non-uniformity that exists in imaging sensors that must be corrected, and non-uniformity in the response of individual pixels. it is not easy to change the fixed pattern noise with tim
- Summary
- Abstract
- Description
- Claims
- Application Information
AI Technical Summary
Benefits of technology
Problems solved by technology
Method used
Image
Examples
Embodiment Construction
[0021]The present invention provides a passive imaging sensor in which at least one optical element comprises one or more Micro-Electro-Mechanical System (MEMS) Micro-Mirror Arrays (MMAs) including a plurality of independently and continuously controllable mirrors that at least tip and tilt in 2 DOF and may tip, tilt and piston in 3 DOF. In an operational mode, the mirrors are tipped and tilted, and possibly pistoned, such that the optical radiation is focused at the pixelated detector to read out an image of the scene. NUC coefficients such as offset and / or gain are applied to either the output signals of the detector or to the image to form the NUC'd images. In a calibration mode, the mirrors are tipped and tilted and / or pistoned to spatially or temporally blur the image or to re-direct the FOV to one or more on-board calibration sources to generate a uniform image from which to calculate and update the NUC coefficients.
[0022]Referring now to FIGS. 1 and 2A-2B, an embodiment of a
PUM
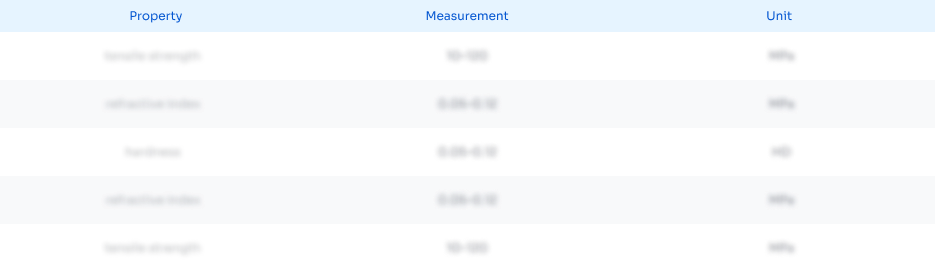
Abstract
Description
Claims
Application Information
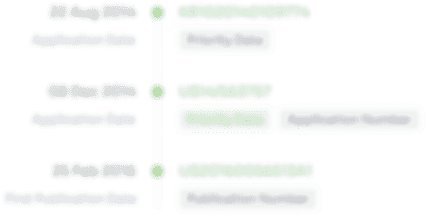
- R&D Engineer
- R&D Manager
- IP Professional
- Industry Leading Data Capabilities
- Powerful AI technology
- Patent DNA Extraction
Browse by: Latest US Patents, China's latest patents, Technical Efficacy Thesaurus, Application Domain, Technology Topic.
© 2024 PatSnap. All rights reserved.Legal|Privacy policy|Modern Slavery Act Transparency Statement|Sitemap