Press welding method for semiconductor extension film
A technology of epitaxial wafers and semiconductors, applied in semiconductor devices, electrical components, circuits, etc., can solve the problems of slow heating rate, long cooling time, and affecting ohmic contact, and achieve fast heating rate, fast heating rate and cooling rate, and improved The effect of production rate
- Summary
- Abstract
- Description
- Claims
- Application Information
AI Technical Summary
Problems solved by technology
Method used
Examples
Example Embodiment
[0023] Construction embodiment one, see figure 1 Shown. First, an ohmic contact layer and a metal bonding layer (ie, a bonding metal to be bonded) are prepared on the InGaAlN epitaxial wafer 101, and an ohmic contact layer and a metal bonding layer are prepared on the substrate 102. If the substrate 102 is metal, there is no need to prepare an ohmic contact layer on the substrate 102. Of course, it is also possible that only the welding surface of the epitaxial wafer or one of the substrates has a pressure welding metal layer. The clamping device for applying pressure to the epitaxial sheet 101 and the substrate 102 includes a pressure member 107 and a pressure member 106. The source of the pressure of the pressing member 107 may be pressure transmitted by air pressure, or pressure transmitted by hydraulic pressure. In order to obtain high-quality welded products, the connection between the pressing member 107 and the pressure source member must be a movable connection such as a uni
Example Embodiment
[0035] Construction embodiment two, such as figure 2 Shown. An epitaxial wafer and a substrate form a pair of welding bodies. The structure of this embodiment is to improve production efficiency. The improved structure in the structure of the first embodiment can be used to weld multiple welding bodies at a time. This structure requires an extended positioning ring 204 and a thickened upper positioning disc 205 and lower positioning disc 203. The pressure member 207, the pressure member 206, and the electromagnetic coil 208 have the same structure as the first embodiment. The welding body composed of the epitaxial wafer 201 and the substrate 202 can be stacked and placed on the workbench for welding. Because the induction current of the electromagnetic coil heats the epitaxial wafer and the substrate, all the epitaxial wafers and the substrate have the same heating rate. The effect is as good as the single welding effect of the embodiment, which greatly improves the welding efficien
PUM
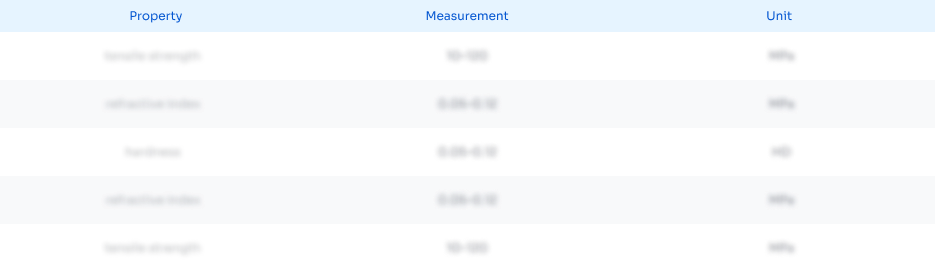
Abstract
Description
Claims
Application Information
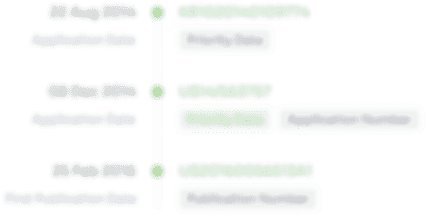
- R&D Engineer
- R&D Manager
- IP Professional
- Industry Leading Data Capabilities
- Powerful AI technology
- Patent DNA Extraction
Browse by: Latest US Patents, China's latest patents, Technical Efficacy Thesaurus, Application Domain, Technology Topic.
© 2024 PatSnap. All rights reserved.Legal|Privacy policy|Modern Slavery Act Transparency Statement|Sitemap