Method for recovering ferrum, vanadium, chromium and gallium from vanadium extraction tailings
A technology for extracting vanadium tailings and recovering iron is applied in the field of metallurgy, which can solve the problems of pollution, waste of resources, environment, and unreasonable utilization, and achieve the effects of reducing environmental pollution, avoiding waste of resources and less equipment.
- Summary
- Abstract
- Description
- Claims
- Application Information
AI Technical Summary
Problems solved by technology
Method used
Image
Examples
example 1
[0028] Example 1 adopts the inventive method to reclaim iron, vanadium, chromium and gallium from vanadium extraction tailings
[0029] Mix vanadium extraction tailings, coal powder, calcium oxide, and binder uniformly in a weight ratio of 100:15:15:2, the particle size of vanadium extraction tailings is -60 mesh, accounting for 86.2%, and the particle size of coal powder is -60 mesh Accounting for 84.2%, the binder is polyvinyl alcohol (PVA). The mixture is pressed into an ellipsoidal green pellet on a powder molding machine, and the maximum radial dimension of the pellet is 15mm. The green pellets were reduced in a rotary hearth furnace with an alkalinity of 1.2, a reduction temperature of 1000°C, and a reduction time of 30 minutes under a CO atmosphere to obtain metallized pellets; the metallized pellets were melted and heated in an electric arc furnace. Deep reduction, the melting temperature is 1450°C, and the melting time is 25 minutes to obtain pig iron and slag containin
example 2
[0030] Example 2 adopts the inventive method to reclaim iron, vanadium, chromium and gallium from vanadium extraction tailings
[0031] The vanadium extraction tailings, coal powder, calcium oxide, and binder are uniformly mixed in a weight ratio of 100:12:17:3, the particle size of the vanadium extraction tailings is -60 mesh, accounting for 86.2%, and the particle size of the coal powder is -60 mesh Accounting for 84.2%, the binder is polyvinyl alcohol (PVA). The mixture is pressed into an ellipsoidal green pellet on a powder molding machine, and the maximum radial dimension of the pellet is 20mm. The raw pellets were reduced in a straight-hearth furnace with an alkalinity of 1.1, under a CO atmosphere, a reduction temperature of 1050°C, and a reduction time of 25 minutes to obtain metallized pellets; the metallized pellets were smelted in a submerged arc furnace And deep reduction, the smelting temperature is 1500°C, and the smelting time is 40 minutes, to obtain pig iron and
example 3
[0032] Example 3 adopts the inventive method to reclaim iron, vanadium, chromium and gallium from vanadium extraction tailings
[0033] The vanadium extraction tailings, coal powder, calcium oxide, and binder are uniformly mixed in a weight ratio of 100:25:15:2, the particle size of the vanadium extraction tailings is -60 mesh, accounting for 86.2%, and the particle size of the coal powder is -60 mesh Accounting for 84.2%, the binder is carboxymethyl cellulose (CMC). The mixture is pressed into pillow-shaped green pellets on a powder molding machine, and the maximum radial dimension of the pellets is 35 mm. The raw pellets were reduced in a straight-hearth furnace with an alkalinity of 1.3, a reduction temperature of 1150°C, and a reduction time of 25 minutes under a CO atmosphere to obtain metallized pellets; the metallized pellets were melted and heated in an electric arc furnace. Deep reduction, the melting temperature is 1600°C, and the melting time is 30 minutes to obtain p
PUM
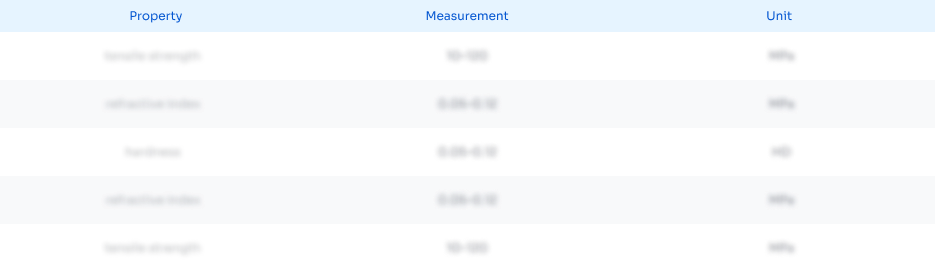
Abstract
Description
Claims
Application Information
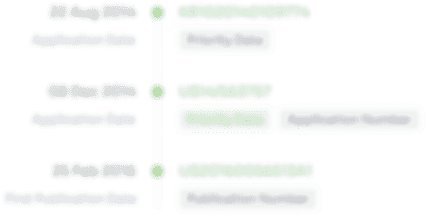
- R&D Engineer
- R&D Manager
- IP Professional
- Industry Leading Data Capabilities
- Powerful AI technology
- Patent DNA Extraction
Browse by: Latest US Patents, China's latest patents, Technical Efficacy Thesaurus, Application Domain, Technology Topic.
© 2024 PatSnap. All rights reserved.Legal|Privacy policy|Modern Slavery Act Transparency Statement|Sitemap