Method for realizing light-weight high-accuracy composite material frame
A composite material and realization method technology, which is applied to space navigation equipment, space navigation aircraft, space navigation equipment, etc., to achieve the effects of small thermal deformation, weight reduction, and improved imaging accuracy
- Summary
- Abstract
- Description
- Claims
- Application Information
AI Technical Summary
Benefits of technology
Problems solved by technology
Method used
Image
Examples
Embodiment Construction
[0018] Preferred embodiments of the present invention will be described below in conjunction with the accompanying drawings.
[0019] figure 1 It is a three-dimensional view of the light-duty high-precision composite material frame of the present invention, figure 2 It is a schematic diagram of the internal structure of the lightweight high-precision composite material frame of the present invention. As shown in the embodiment of the accompanying drawings, the device includes:
[0020] Rectangular section bar [1], joint [2], joint gasket [3], joint bushing [4], bar embedded part [5]; the whole structure consists of a certain number of rectangular section bars [1] and joints [2] Form the main body of the framework. The rod with rectangular cross section [1] is internally glued with a rod embedded part [5], the outer surface of the joint [2] is glued to the joint gasket [3], and the inner glued joint bushing [4].
[0021] The rectangular section bar [1] is a carbon / epoxy com
PUM
Property | Measurement | Unit |
---|---|---|
Wall thickness | aaaaa | aaaaa |
Wall thickness | aaaaa | aaaaa |
Abstract
Description
Claims
Application Information
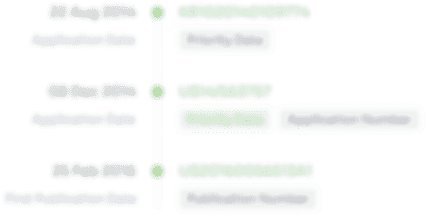
- R&D Engineer
- R&D Manager
- IP Professional
- Industry Leading Data Capabilities
- Powerful AI technology
- Patent DNA Extraction
Browse by: Latest US Patents, China's latest patents, Technical Efficacy Thesaurus, Application Domain, Technology Topic.
© 2024 PatSnap. All rights reserved.Legal|Privacy policy|Modern Slavery Act Transparency Statement|Sitemap