Purification method of nano diamond ash material
A technology of nano-diamond and purification method, which is applied in the field of joint removal of graphite carbon, metal oxide and silicon dioxide impurities. The effect of simple process, low equipment requirements and high product purity
- Summary
- Abstract
- Description
- Claims
- Application Information
AI Technical Summary
Problems solved by technology
Method used
Image
Examples
Embodiment 1
[0014] Embodiment 1: purify nano-diamond dust material according to the following steps
[0015] (1) Removal of metal impurities: In a 50L reaction kettle, add 25.0kg of 20% nitric acid, add 5.00kg of nano-diamond ash material under stirring, and heat up to 70 o C, stirred for 48h, cooled to room temperature, vacuum filtered, and fully washed with deionized water to neutrality, the solid matter at 80 o C is vacuum-dried to obtain 4.22kg of a purified product; yield 84.4%;
[0016] (2) Removal of graphite carbon impurities: In a 50L reactor, put 10.0kg of sulfuric acid with a mass concentration of 98%, add 3.00kg of a purified product under stirring, and heat up to 250 under vacuum o C, dropwise add 16.0kg of mass concentration 70% perchloric acid, control the temperature in the kettle to 200°C during the dropwise addition process o C, the dropwise addition was completed in 8 hours, and then 250 o C for 1 hour, cool to 40 o C, poured into 50L deionized water, filtered, and ful
Embodiment 2
[0018] Embodiment 2: purify nano-diamond dust material according to the following steps
[0019] (1) Removal of metal impurities: In a 50L reaction kettle, add 40.0kg of 5% nitric acid, add 5.00kg of nano-diamond ash material under stirring, and heat up to 95 o C, stirred for 1h, cooled to room temperature, vacuum filtered, and fully washed with deionized water to neutrality, the solid matter at 80 o C is vacuum-dried to obtain 4.02kg of a purified product; yield 80.4%;
[0020] (2) Removal of graphite carbon impurities: In a 50L reactor, put 15.0kg of sulfuric acid with a mass concentration of 94%, add 1.00kg of a purified product under stirring, and heat up to 180 under vacuum o C, dropwise add 55% perchloric acid with a mass concentration of 20.0kg, and control the temperature in the kettle to 180-230°C during the dropwise addition process o C, the dropwise addition was completed in 7 hours, and then 210 o C for 5 hours, cool to 40 o C, poured into 60L deionized water, fil
Embodiment 3
[0022] Embodiment 3: purify nano-diamond dust material according to the following steps
[0023] (1) Removal of metal impurities: In a 50L reactor, add 20.0kg of 50% nitric acid, add 4.00kg of nano-diamond ash material under stirring, and control the temperature for 10 o C, stirred for 24h, cooled to room temperature, vacuum filtered, and fully washed with deionized water to neutrality, the solid matter at 80 o C is vacuum-dried to obtain 3.66kg of a purified product; yield 91.5%;
[0024] (2) Removal of graphite carbon impurities: In a 50L reactor, put 40kg of sulfuric acid with a mass concentration of 90%, add 2.00kg of a purified product under stirring, and heat up to 180 under vacuum o C, dropwise add 15kg of 40% perchloric acid in mass concentration, and control the temperature in the kettle to 170-210°C during the dropwise addition process o C, then 180 o C for 10 hours, cool to 40 o C, poured into 100L deionized water, filtered, and fully washed with deionized water un
PUM
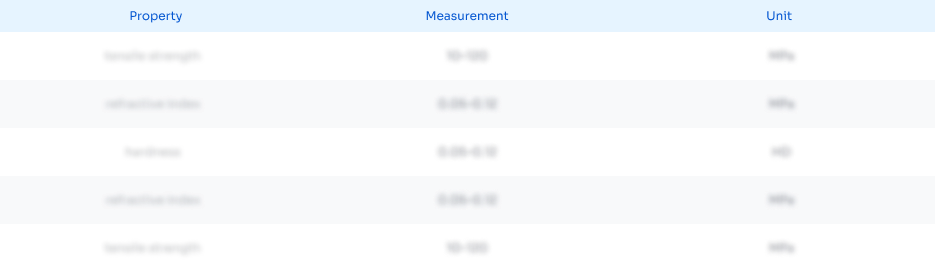
Abstract
Description
Claims
Application Information
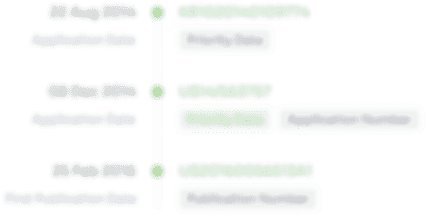
- R&D Engineer
- R&D Manager
- IP Professional
- Industry Leading Data Capabilities
- Powerful AI technology
- Patent DNA Extraction
Browse by: Latest US Patents, China's latest patents, Technical Efficacy Thesaurus, Application Domain, Technology Topic.
© 2024 PatSnap. All rights reserved.Legal|Privacy policy|Modern Slavery Act Transparency Statement|Sitemap