Plant fiber fireproofing silencing plate
A plant fiberboard and plant fiber technology, applied in the field of sound-absorbing panels, can solve the problems of non-fireproof and sound-absorbing effects of the panels, and achieve the effects of low cost, easy processing, and added fireproof performance
- Summary
- Abstract
- Description
- Claims
- Application Information
AI Technical Summary
Benefits of technology
Problems solved by technology
Method used
Examples
Embodiment 1
[0029] The plant fiber fireproof and sound-absorbing board of this embodiment includes a plant fiber board and a cover, and the cover is attached to at least one side of the plant fiber board; the cover can be made of wood veneer, metal sheet or plastic, etc., to cover the plant fiber board on the one hand, making it beautiful Generous, on the other hand, it protects the plant fiberboard;
[0030] The manufacturing process of described plant fiberboard comprises the steps:
[0031] A, take coconut palm fiber as raw material to make slab by paving process, the density of slab is 0.10g / cm3;
[0032] B. Immerse the slab in an inorganic gelling slurry consisting of magnesium chloride, magnesium oxide and water with a mass percentage concentration of 50%, and the soaking time is 5 to 10 minutes;
[0033] C, the slab after soaking is sent into the roll pressing machine, and the density of the plate after pressing is 0.4g / cm3;
[0034] D. The rolled board is cured and dried, and t
Embodiment 2
[0056] The plant fiber fireproof and sound-absorbing board of this embodiment is different from Embodiment 1 in that the manufacturing process of the plant fiber board includes the following steps:
[0057] A, take coconut palm fiber as raw material to make slab by paving process, the density of slab is 0.12g / cm3;
[0058] B. Immerse the slab in an inorganic gelling slurry consisting of magnesium chloride, magnesium oxide and water with a mass percentage concentration of 70%, and the soaking time is 5 to 10 minutes;
[0059] C, the slab after soaking is sent to roll pressing in the pressure roller machine, the density of the plate after pressing is 0.6g / cm3;
[0060] D. The rolled board is cured and dried, and the veneer is cut to make the plant fiber board.
[0061] In the step C, the pressure of the pressure roller is 2000N / cm.
Embodiment 3
[0063] The plant fiber fireproof and sound-absorbing board of this embodiment is different from Embodiment 1 in that the manufacturing process of the plant fiber board includes the following steps:
[0064] A, take coconut palm fiber as raw material to make slab by paving process, the density of slab is 0.11g / cm3;
[0065] B, immersing the slab in an inorganic gelling slurry of 60% mass percentage concentration composed of magnesium chloride, magnesium oxide and water, soaking time is 8 minutes;
[0066] C, the slab after soaking is sent to roll pressing in the pressure roller machine, the density of the plate after pressing is 0.5g / cm3;
[0067] D. The rolled board is cured and dried, and the veneer is cut to make the plant fiber board.
[0068] In the step C, the pressure of the pressure roller is 1700N / cm.
PUM
Property | Measurement | Unit |
---|---|---|
Density | aaaaa | aaaaa |
Density | aaaaa | aaaaa |
Density | aaaaa | aaaaa |
Abstract
Description
Claims
Application Information
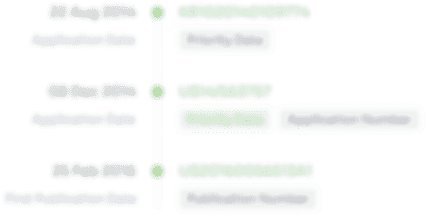
- R&D Engineer
- R&D Manager
- IP Professional
- Industry Leading Data Capabilities
- Powerful AI technology
- Patent DNA Extraction
Browse by: Latest US Patents, China's latest patents, Technical Efficacy Thesaurus, Application Domain, Technology Topic.
© 2024 PatSnap. All rights reserved.Legal|Privacy policy|Modern Slavery Act Transparency Statement|Sitemap