Plating method for anti-reflection film with high transmittance and low reflectivity
A low-reflectivity, anti-reflection film technology, applied in sputtering plating, ion implantation plating, vacuum evaporation plating, etc., can solve low transmittance, high reflectivity, AR film spectral curve can not meet customer requirements To achieve the effect of improving the transmittance, ensuring the service life, and avoiding the drift of the spectroscopic curve of the finished product
- Summary
- Abstract
- Description
- Claims
- Application Information
AI Technical Summary
Benefits of technology
Problems solved by technology
Method used
Image
Examples
Embodiment Construction
[0033] Below in conjunction with accompanying drawing and embodiment the present invention will be further described.
[0034] A method for coating an anti-reflection film with high transmittance and low reflectivity, which is completed in a vacuum coating device by the following steps:
[0035] (1) Conventional vacuuming steps;
[0036] (2), conventional heating steps;
[0037] (3), Ar+O 2 The ion cleaning step;
[0038] (4) Coating SiO on the film 2 ;
[0039] (5) Etching in a full oxygen atmosphere, the pressure in the furnace can be the same as that of the coating stage, and the time is generally 2-5 minutes; at the same time, the pulse power is used as the ion activation treatment of the ion source power, so that under the action of the pulse electric field, the surface of the lens The vibration of the original low-priced ions intensifies, the degree of activity increases, and it is easier to further lose electrons, forming a strong and stable chemical bond structure wi
PUM
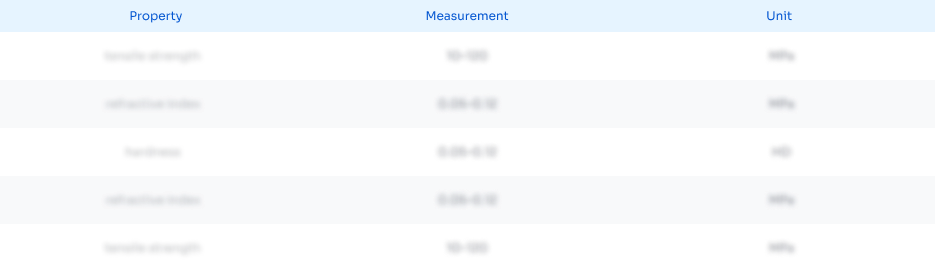
Abstract
Description
Claims
Application Information
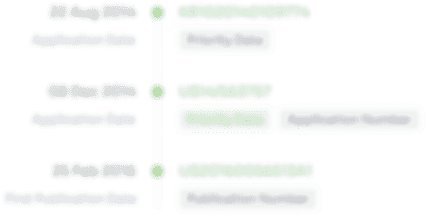
- R&D Engineer
- R&D Manager
- IP Professional
- Industry Leading Data Capabilities
- Powerful AI technology
- Patent DNA Extraction
Browse by: Latest US Patents, China's latest patents, Technical Efficacy Thesaurus, Application Domain, Technology Topic.
© 2024 PatSnap. All rights reserved.Legal|Privacy policy|Modern Slavery Act Transparency Statement|Sitemap