Production process of novel heat insulation cast electrophoresis aluminium section structure
A production process, casting technology, applied in the direction of the wing frame and other directions, can solve the problems of chemical bonding and poor physical bonding performance.
- Summary
- Abstract
- Description
- Claims
- Application Information
AI Technical Summary
Problems solved by technology
Method used
Image
Examples
Embodiment Construction
[0024] Such as figure 1 and image 3 Shown, the production technology of a kind of novel heat-insulating casting type electrophoresis aluminum profile structure of the present invention; It comprises the following steps:
[0025] S1: extruded end face profile: extruded profile 1, the obtained profile 1 has a glue injection groove 2 sealed by the sealing profile 3;
[0026] S2: surface treatment: in step 1, the outer surface of the profile 1 with the closed glue injection tank 2 is fully electrophoretic painted;
[0027] S3: profile tearing: tear off the sealing profile 3 that seals the glue injection tank 2 with clamps such as pliers, and obtain the glue injection tank 2 without electrophoretic paint coating on the inner wall;
[0028] S4: Profile glue injection: inject glue into the glue injection groove 2 that has no electrophoretic paint coating on the inner wall.
[0029] Through the combined use of the ingot cylinder and the extrusion die, a glue injection tank 2 with a
PUM
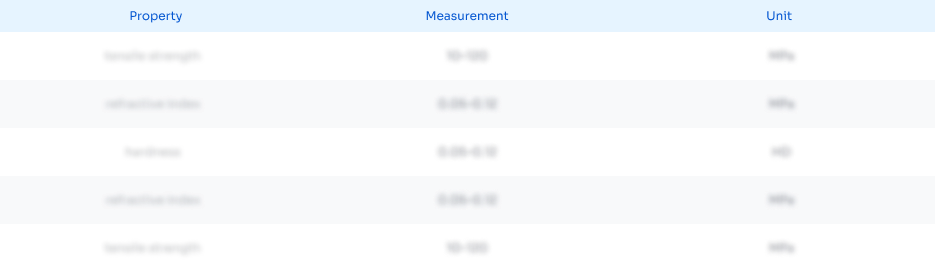
Abstract
Description
Claims
Application Information
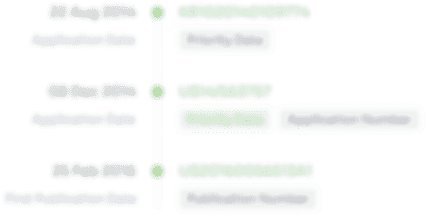
- R&D Engineer
- R&D Manager
- IP Professional
- Industry Leading Data Capabilities
- Powerful AI technology
- Patent DNA Extraction
Browse by: Latest US Patents, China's latest patents, Technical Efficacy Thesaurus, Application Domain, Technology Topic.
© 2024 PatSnap. All rights reserved.Legal|Privacy policy|Modern Slavery Act Transparency Statement|Sitemap