Zn1-xMgxO group heterojunction and preparation method thereof
A zn1-xmgxo, 01-xmgxo technology, applied in the field of wide bandgap semiconductor optoelectronic devices, can solve the problems of difficult preparation of thin film materials and non-adjustable bandgap width of thin film layers
- Summary
- Abstract
- Description
- Claims
- Application Information
AI Technical Summary
Benefits of technology
Problems solved by technology
Method used
Image
Examples
Embodiment 1
[0022] 1) Weigh ZnO, MgO and Al with purity ≥99.99% 2 o 3 Powder, wherein the molar percentage x of Mg is 10%, and the molar percentage a of Al is 2%. The above-mentioned powder and an appropriate amount of ethanol are poured into a ball mill jar equipped with agate balls successively, and placed on a ball mill for ball milling for 24 Hours. There are two purposes of ball milling: on the one hand, it is to combine ZnO, MgO and Al 2 o 3 The powder is mixed evenly to ensure the uniformity of the target material composition; on the other hand, it is to mix ZnO, MgO and Al 2 o 3 The powder is refined to facilitate the subsequent molding and sintering of the mixed powder. After ball milling, the raw materials are separated and dried, and the resulting powder is ground and pressed into shape. Put the formed green body into a sintering furnace, pre-sinter at 800 °C for 1 hour, and then sinter at 1100-1200 °C for more than 8 hours to obtain an Al-doped Zn alloy with a thickness of
Embodiment 2
[0027] 1) Weigh ZnO, MgO and Ga with purity ≥99.99% 2 o 3 Powder, wherein the molar percentage x of Mg is 20%, and the molar percentage a of Al is 3%. The above-mentioned powder and an appropriate amount of ethanol are poured into a ball mill jar equipped with agate balls successively, and placed on a ball mill for ball milling for 24 Hours. There are two purposes of ball milling: on the one hand, it is to combine ZnO, MgO and Al 2 o 3 The powder is mixed evenly to ensure the uniformity of the target material composition; on the other hand, it is to mix ZnO, MgO and Al 2 o 3 The powder is refined to facilitate the subsequent molding and sintering of the mixed powder. After ball milling, the raw materials are separated and dried, and the resulting powder is ground and pressed into shape. Put the formed green body into a sintering furnace, pre-sinter at 800 °C for 1 hour, and then sinter at 1100-1200 °C for more than 8 hours to obtain an Al-doped Zn alloy with a thickness of
Embodiment 3
[0032] 1) Weigh ZnO, MgO and Al with purity ≥99.99% 2 o 3 Powder, wherein the molar percentage x of Mg is 30%, and the molar percentage a of Al is 4%. The above-mentioned powder and an appropriate amount of ethanol are poured into a ball mill jar equipped with agate balls successively, and placed on a ball mill for ball milling for 24 Hours. There are two purposes of ball milling: on the one hand, it is to combine ZnO, MgO and Al 2 o 3 The powder is mixed evenly to ensure the uniformity of the target material composition; on the other hand, it is to mix ZnO, MgO and Al 2 o 3 The powder is refined to facilitate the subsequent molding and sintering of the mixed powder. After ball milling, the raw materials are separated and dried, and the resulting powder is ground and pressed into shape. Put the molded green body into the sintering furnace, pre-sinter at 800 °C for 1 hour, and then sinter at 1100-1200 °C for more than 8 hours to obtain Al-doped Zn with a thickness of about 3
PUM
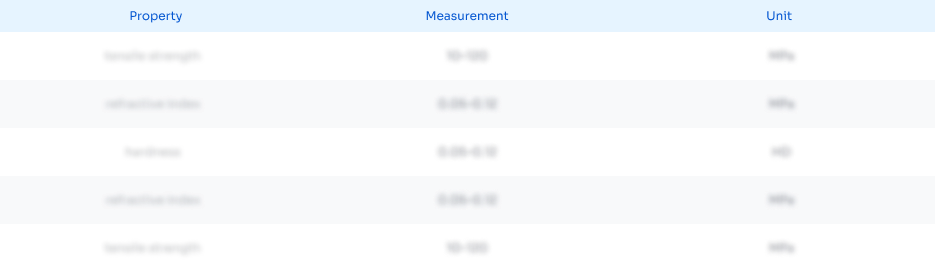
Abstract
Description
Claims
Application Information
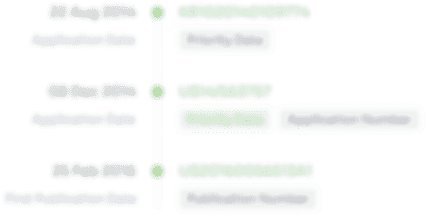
- R&D Engineer
- R&D Manager
- IP Professional
- Industry Leading Data Capabilities
- Powerful AI technology
- Patent DNA Extraction
Browse by: Latest US Patents, China's latest patents, Technical Efficacy Thesaurus, Application Domain, Technology Topic.
© 2024 PatSnap. All rights reserved.Legal|Privacy policy|Modern Slavery Act Transparency Statement|Sitemap