Permeable filtering sound insulation material and manufacturing method thereof, tray, decorative brick and filtering equipment
A technology of sound insulation material and manufacturing method, which is applied in the field of new building materials, can solve the problems of damaged surface layer, no sound insulation function, impermeability, etc., and achieve the effect of low cost and maintaining delicate and beautiful appearance
- Summary
- Abstract
- Description
- Claims
- Application Information
AI Technical Summary
Benefits of technology
Problems solved by technology
Method used
Image
Examples
Embodiment 1
[0102] The raw materials include 10 kg of quartz sand, 5 kg of quartz powder, 5 kg of activated carbon, and 3 kg of epoxy resin glue (A glue and B glue are not mixed). Among them, the mass ratio of glue A and glue B is 1:3, the particle size of quartz sand is 80 mesh, and the particle size of quartz powder is 300 mesh. In a separate oven, bake the quartz sand and quartz powder mixture at a temperature of about 200 degrees Celsius for about 4 hours. In another oven, bake the A glue and the B glue of the epoxy resin at about 120 degrees Celsius for about 4 hours. Pour the baked quartz sand, quartz powder, epoxy resin glue and cement powder pigment into a mixer, and stir evenly to form a mixture of quartz particles and epoxy resin glue. Put the mixture of quartz particles and epoxy resin back into the oven and spread it evenly, bake at about 120 degrees Celsius for about 4 hours. The solidified mixture obtained after the second baking is put into a crusher for crushing, breaking t
Embodiment 2
[0104] The raw materials include 15 kg of quartz sand, 5 kg of quartz powder, and 4 kg of epoxy resin glue (A glue and B glue are not mixed). Among them, the mass ratio of glue A and glue B is 1:3, the particle size of quartz sand is 100 mesh, and the particle size of quartz powder is 400 mesh. In a separate oven, bake the quartz sand and quartz powder mixture at about 300 degrees Celsius for about 2 hours. In another oven, bake the A glue and the B glue of the epoxy resin at about 150 degrees Celsius for about 3 hours. Pour the baked quartz sand, quartz powder, epoxy resin glue and cement powder pigment into a mixer, and stir evenly to form a mixture of quartz particles and epoxy resin glue. Put the mixture of quartz particles and epoxy resin back into the oven and spread it evenly, bake at about 150 degrees Celsius for about 3 hours. The solidified mixture obtained after the second baking is put into a crusher for crushing, breaking the mixture into small pieces. The crushed
Embodiment 3
[0106] The raw materials include 20 kg of quartz sand and 6 kg of epoxy resin glue (A glue and B glue are not mixed). Among them, the mass ratio of glue A and glue B is 1:3, and the particle size of quartz sand is 120 mesh. In a separate oven, bake the quartz sand at about 150 degrees Celsius for about 8 hours. In another oven, bake the A glue and the B glue of the epoxy resin at about 100 degrees Celsius for about 5 hours. Pour the baked quartz sand, epoxy resin glue and cement powder pigment into a mixer, and stir evenly to form a mixture of quartz particles and epoxy resin glue. Put the mixture of quartz particles and epoxy resin back into the oven and spread it evenly, bake at about 200 degrees Celsius for about 2 hours. The solidified mixture obtained after the second baking is put into a crusher for crushing, breaking the mixture into small pieces. The crushed material is put into a ball mill and ball milled into powder. Use a sieve to screen the ground quartz particles
PUM
Property | Measurement | Unit |
---|---|---|
Particle size | aaaaa | aaaaa |
Particle size | aaaaa | aaaaa |
Particle size | aaaaa | aaaaa |
Abstract
Description
Claims
Application Information
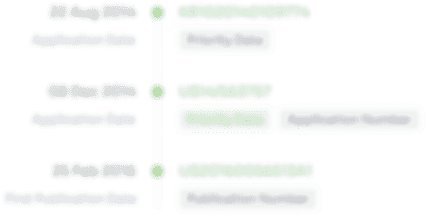
- R&D Engineer
- R&D Manager
- IP Professional
- Industry Leading Data Capabilities
- Powerful AI technology
- Patent DNA Extraction
Browse by: Latest US Patents, China's latest patents, Technical Efficacy Thesaurus, Application Domain, Technology Topic.
© 2024 PatSnap. All rights reserved.Legal|Privacy policy|Modern Slavery Act Transparency Statement|Sitemap