Method for preparing high-temperature resistant microporous membrane
A microporous membrane, high temperature resistant technology, applied in the direction of electrical components, circuits, battery pack components, etc., can solve the problems of battery safety hazards, easy to block the diaphragm, and inability to obtain consistency, etc., to solve compatibility problems, Solve the effect of mechanical property degradation
- Summary
- Abstract
- Description
- Claims
- Application Information
AI Technical Summary
Benefits of technology
Problems solved by technology
Method used
Examples
Embodiment 1
[0024] A method for preparing a high-temperature-resistant microporous membrane, the method for preparing comprises the following steps in sequence:
[0025] A, 40kg resin mixture and 160kg paraffin oil will be added to the twin-screw extruder through a feeding port and mixed uniformly. The resin mixture is made up of 0.8kg polyester, 2kg polypropylene and 37.2kg polyethylene, polyester Melting point greater than 170 ° C, polyethylene contains 3.72kg molecular weight greater than 10 6 Polyethylene, the average molecular weight of polyethylene is 2.5×10 5 ~1.5×10 6 , the average molecular weight of polypropylene is 2×10 4 ~10 6 And the melting point is greater than 145°C;
[0026] B. The raw materials mixed in step A are melted and extruded through the die of the extruder at 170 ° C, and naturally cooled to form a sheet;
[0027] C. The sheet in step B is first stretched vertically five times and then stretched horizontally by the roller. The total s
Embodiment 2
[0032] A method for preparing a high-temperature-resistant microporous membrane, the method for preparing comprises the following steps in sequence:
[0033] A. Mix 40kg of resin mixture and 126.4kg of paraffin oil raw materials. The resin mixture is composed of 2.4kg of polyamide, 4kg of polypropylene and 33.6kg of polyethylene. The melting point of polyamide is greater than 170°C, and polyethylene contains 7.44kg of molecular weight 10 6 Polyethylene, the average molecular weight of polyethylene is 2.5×10 5 ~1.5×10 6 , the average molecular weight of polypropylene is 2×10 4 ~10 6 And the melting point is greater than 145°C. The mixing process is as follows: ① Mix 2.4kg polyamide, 4kg polypropylene and 16.8kg polyethylene in a high-speed dispersion to form a material, ② Mix the remaining 16.8kg polyethylene with 63.2kg paraffin oil Mix it into material b, ③, add material a into material b and mix it into material c, ④, add material c and the remaining 6
Embodiment 3
[0040] A method for preparing a high-temperature-resistant microporous membrane, the method for preparing comprises the following steps in sequence:
[0041] A. Mix 40kg of resin mixture and 32.8kg of paraffin oil in a kneader and add them to the extruder. The resin mixture is composed of 4kg of polymethylpentene, 6kg of polypropylene and 30kg of polyethylene. Polymethylpentene The melting point of alkene is greater than 170°C, and polyethylene contains 27.9kg of molecular weight greater than 10 6 Polyethylene, the average molecular weight of polyethylene is 2.5×10 5 ~1.5×10 6 , the average molecular weight of polypropylene is 2×10 4 ~10 6 And the melting point is greater than 145°C;
[0042] B. Melt and extrude the raw materials mixed in step A through the die head of the extruder at 250°C, and cool with a roller at a cooling rate of 80°C / s to form a sheet, and the cooling medium is water;
[0043] C, the sheet material of step B is stretched hor
PUM
Property | Measurement | Unit |
---|---|---|
Melting point | aaaaa | aaaaa |
Melting point | aaaaa | aaaaa |
Abstract
Description
Claims
Application Information
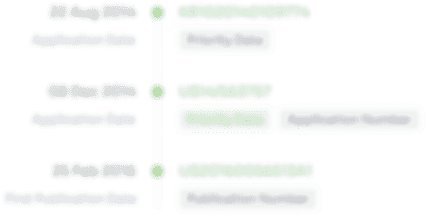
- R&D Engineer
- R&D Manager
- IP Professional
- Industry Leading Data Capabilities
- Powerful AI technology
- Patent DNA Extraction
Browse by: Latest US Patents, China's latest patents, Technical Efficacy Thesaurus, Application Domain, Technology Topic.
© 2024 PatSnap. All rights reserved.Legal|Privacy policy|Modern Slavery Act Transparency Statement|Sitemap