Melt electrostatic spinning sprayer suitable for high-viscosity high-melting-point polymers
A melt electrospinning, high melting point technology, used in textiles and papermaking, filament/thread forming, fiber processing, etc. Process conditions, the effect of avoiding clogging
- Summary
- Abstract
- Description
- Claims
- Application Information
AI Technical Summary
Problems solved by technology
Method used
Image
Examples
Example Embodiment
[0018] The present invention provides a melt electrospinning nozzle suitable for high-viscosity and high-melting polymers. Such as Figure 1-5 As shown, the spinning device mainly includes a spinning nozzle 1, a spinning nozzle set 2, a nozzle sleeve 3, a plunger 4, a weight plate 5, a heating device 6, a temperature sensor 7, and an elastic sealing ring 8. The spinning nozzle 1 and the spinning nozzle kit 2 and the upper part of the nozzle kit 2 and the nozzle sleeve 3 are all screwed together, and can be automatically centered by concentricity during installation. The plunger 4 is placed inside the nozzle sleeve 3, The upper end of the counterweight plate 5 is threadedly connected to apply pressure to the melt in the sleeve. The nozzle sleeve 3 is fixed on the spinning frame through evenly distributed bolt holes 3-1, and the heating device 6 is placed on the nozzle The periphery of the sleeve 3 can be easily disassembled. The temperature sensor 7 is placed inside the nozzle sle
PUM
Property | Measurement | Unit |
---|---|---|
Diameter | aaaaa | aaaaa |
Abstract
Description
Claims
Application Information
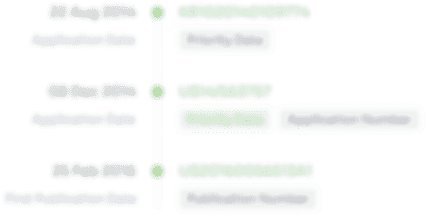
- R&D Engineer
- R&D Manager
- IP Professional
- Industry Leading Data Capabilities
- Powerful AI technology
- Patent DNA Extraction
Browse by: Latest US Patents, China's latest patents, Technical Efficacy Thesaurus, Application Domain, Technology Topic.
© 2024 PatSnap. All rights reserved.Legal|Privacy policy|Modern Slavery Act Transparency Statement|Sitemap