Preparation method of carbon nano-tube/amorphous carbon/epoxy resin composite material
A carbon nanotube and epoxy resin technology, applied in the synthesis and application of carbon nanocomposite materials, can solve the problems of carbon nanotube agglomeration and winding, affecting the effect of carbon nanotube on resin modification, etc., and achieve the improvement of strength and modulus , excellent mechanical properties, enhanced effect of epoxy resin
- Summary
- Abstract
- Description
- Claims
- Application Information
AI Technical Summary
Problems solved by technology
Method used
Examples
Embodiment 1
[0020] The preparation method of carbon nanotube / amorphous carbon / epoxy resin composite material in the present embodiment is realized according to the following steps:
[0021] 1. Place the clean quartz substrate in the middle of the quartz reaction chamber of the high-temperature furnace, then seal the quartz reaction chamber, adjust the heating program and start to heat up; during the heating process, 800mL / min of argon gas is introduced to remove the air in the reaction chamber to maintain the atmosphere Stable; when the temperature rises to 820~940℃, adjust the argon gas flow rate to 2000mL / min, and introduce hydrogen gas at 100~500mL / min, turn on the precision syringe pump, and inject dihydrogen at a concentration of 20~100mg / mL into the reaction chamber Ferrocene / dichlorobenzene carbon source reaction solution, the feed rate is 0.1~0.3mL / min, and the reaction time is 0.5~4h. Subsequently, stop feeding the ferrocene / dichlorobenzene carbon source reaction s
Embodiment 2
[0026] The preparation method of carbon nanotube / amorphous carbon / epoxy resin composite material in the present embodiment is realized according to the following steps:
[0027] 1. Place the clean quartz substrate in the middle of the quartz reaction chamber of the high-temperature furnace, then seal the quartz reaction chamber, adjust the heating program and start to heat up; during the heating process, 800mL / min of argon gas is introduced to remove the air in the reaction chamber to maintain the atmosphere Stable; when the temperature rises to 880°C, adjust the flow rate of argon to 2000mL / min, and inject 300mL / min of hydrogen, turn on the precision syringe pump, and inject ferrocene / dichlorobenzene with a concentration of 60mg / mL into the reaction chamber Carbon source reaction solution, the feed rate is 0.1mL / min, and the reaction time is 2h. Subsequently, stop feeding the ferrocene / dichlorobenzene carbon source reaction solution and turn off the hydrogen, a
Embodiment 3
[0031]The preparation method of carbon nanotube / amorphous carbon / epoxy resin composite material in the present embodiment is realized according to the following steps:
[0032] 1. Place the clean quartz substrate in the middle of the quartz reaction chamber of the high-temperature furnace, then seal the quartz reaction chamber, adjust the heating program and start to heat up; during the heating process, 800mL / min of argon gas is introduced to remove the air in the reaction chamber to maintain the atmosphere Stable; when the temperature rises to 880°C, adjust the flow rate of argon to 2000mL / min, and inject 300mL / min of hydrogen, turn on the precision syringe pump, and inject ferrocene / dichlorobenzene with a concentration of 60mg / mL into the reaction chamber Carbon source reaction solution, the feed rate is 0.1mL / min, and the reaction time is 2h. Subsequently, stop feeding the ferrocene / dichlorobenzene carbon source reaction solution and turn off the hydrogen, an
PUM
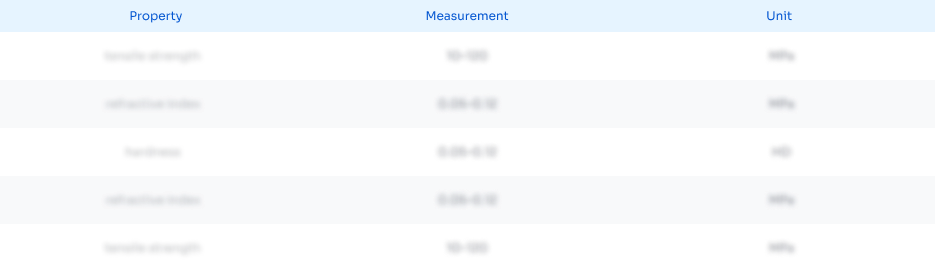
Abstract
Description
Claims
Application Information
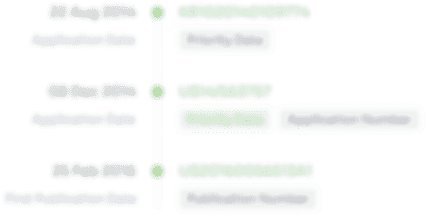
- R&D Engineer
- R&D Manager
- IP Professional
- Industry Leading Data Capabilities
- Powerful AI technology
- Patent DNA Extraction
Browse by: Latest US Patents, China's latest patents, Technical Efficacy Thesaurus, Application Domain, Technology Topic.
© 2024 PatSnap. All rights reserved.Legal|Privacy policy|Modern Slavery Act Transparency Statement|Sitemap