Production process of jacket
A production process and jacket technology, applied in the field of jacket production technology, can solve the problems of increased cost, large cost burden of enterprises, high scrap rate of jacket, and achieve the effect of strong bearing capacity, lower production cost and material saving.
- Summary
- Abstract
- Description
- Claims
- Application Information
AI Technical Summary
Problems solved by technology
Method used
Image
Examples
Example Embodiment
[0023] refer to Figure 1 to Figure 3 As shown in the figure, the production process of a jacket in this embodiment includes the following steps: material preparation: punching and cutting the copper material into strips according to the designed size; multiple stretching: placing the prepared strips in a continuous mold Stretching is performed in sequence; punching: the stretched jacket is placed in the stamping die on the continuous die for punching; ring extrusion: the punched jacket is placed in the extrusion die on the continuous die for ring extrusion ;Stretching: Put the extruded jacket into the stretching die and stretch again, so that the diameter of the stretched jacket is between 5 mm and 5.2 mm; Shaping and flattening; easy to cut: easy to cut the shaped jacket; drop product: the easy-to-cut jacket falls off on the continuous die.
[0024] By adopting the above technical scheme, the production process of a jacket includes the steps of material preparation, multiple s
PUM
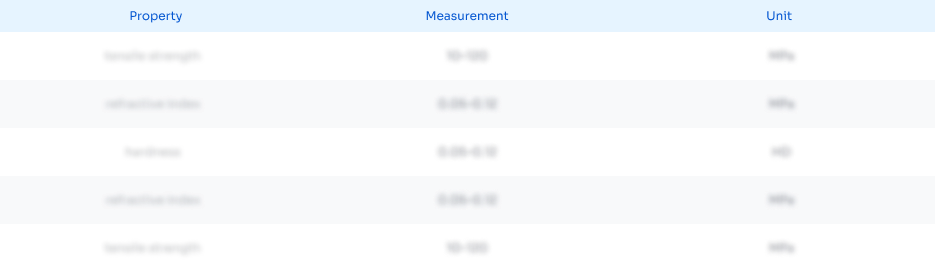
Abstract
Description
Claims
Application Information
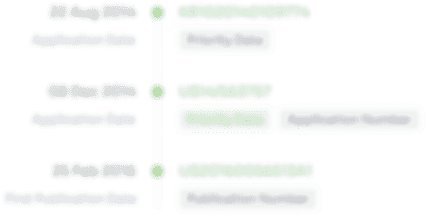
- R&D Engineer
- R&D Manager
- IP Professional
- Industry Leading Data Capabilities
- Powerful AI technology
- Patent DNA Extraction
Browse by: Latest US Patents, China's latest patents, Technical Efficacy Thesaurus, Application Domain, Technology Topic.
© 2024 PatSnap. All rights reserved.Legal|Privacy policy|Modern Slavery Act Transparency Statement|Sitemap