Production method for preparing polyvinyl chloride fibers for hair by melting method
A technology of polyvinyl chloride fiber and production method, applied in the direction of fiber chemical characteristics, application, wigs, etc., can solve the problems such as the decline of the use performance of PVC fiber, the migration of small molecules of processing aids, and the influence of product strength, so as to reduce shrinkage, The effect of avoiding small molecule migration and improving dimensional stability
- Summary
- Abstract
- Description
- Claims
- Application Information
AI Technical Summary
Benefits of technology
Problems solved by technology
Method used
Image
Examples
Embodiment 1
[0027] 100 parts by weight of PVC resin, 35 parts of DOP, 15 parts of DBP, 3 parts of organotin heat stabilizer, 3 parts of glyceryl monostearate and 1.5 parts of tetrakis[β-(3,5-di-tert-butyl- 4-Hydroxyphenyl) propionic acid] pentaerythritol ester was plasticized and mixed for 30 minutes, and the mixed material was plasticized, melted and spun through a screw extruder. °C, the temperature in the third zone is 188°C, the temperature in the fourth zone is 182°C, the screw speed is 20r / min, and the spinning speed is 30m / min.
[0028] The extruded PVC fiber is post-stretched, the stretching ratio is 4 times, and then the obtained fiber is treated with ether, the weight ratio of ether and PVC fiber is 9:1, the processing time is 45min, and finally the finished product is obtained after 4 times stretching PVC fibers.
[0029] After testing, the amount of plasticizer extracted with ether is 28.5%; the amount of residual plasticizer in the fiber is 4.8%, and the shrinkage rate is 4
Embodiment 2
[0031] 100 parts by weight of PVC resin, 40 parts of DOP, 20 parts of DBP, 3 parts of organotin heat stabilizer, 3 parts of glyceryl monostearate and 1.5 parts of tetrakis[β-(3,5-di-tert-butyl- 4-Hydroxyphenyl)propionic acid]pentaerythritol ester is plasticized and mixed, and the mixed material is plasticized, melted and spun through a screw extruder. The temperature of the first zone of the screw extruder is 150°C, and the temperature of the second zone is 175°C. , the temperature in the third zone is 185°C, the temperature in the fourth zone is 180°C, the screw speed is 25r / min, and the spinning speed is 35m / min.
[0032] The extruded PVC fiber was post-stretched, the stretching ratio was 5 times, and then the obtained fiber was treated with ether, the weight ratio of ether and PVC fiber was 10:1, the treatment time was 45 min, and finally stretched 5 times to obtain Finished PVC fiber.
[0033] After testing, the amount of plasticizer extracted with ether was 32.6%; the a
Embodiment 3
[0035] 100 parts by weight of PVC resin, 45 parts of DOP, 25 parts of DBP, 3 parts of organotin heat stabilizer, 3 parts of glyceryl monostearate and 1.5 parts of tetrakis[β-(3,5-di-tert-butyl- 4-Hydroxyphenyl)propionic acid]pentaerythritol ester is plasticized and mixed, and the mixed material is plasticized, melted and spun through a screw extruder. The temperature of the first zone of the screw extruder is 150°C, and the temperature of the second zone is 170°C. , the temperature in the third zone is 180°C, the temperature in the fourth zone is 175°C, the screw speed is 20r / min, and the spinning speed is 35m / min.
[0036] The extruded PVC fiber is post-stretched, the stretching ratio is 4 times, and then the obtained fiber is treated with ether, the weight ratio of ether and PVC fiber is 10:1, the treatment time is 1h, and finally the finished product is obtained after 4 times stretching PVC fibers.
[0037] After testing, the amount of plasticizer extracted with ether was
PUM
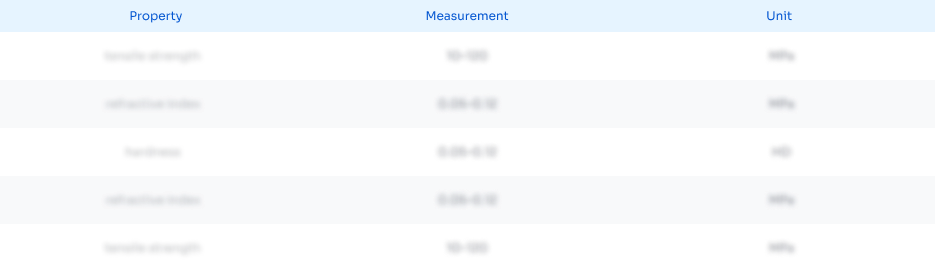
Abstract
Description
Claims
Application Information
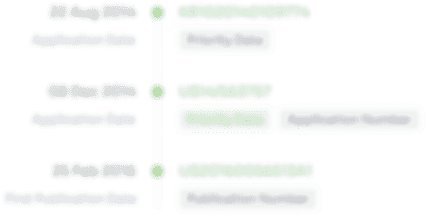
- R&D Engineer
- R&D Manager
- IP Professional
- Industry Leading Data Capabilities
- Powerful AI technology
- Patent DNA Extraction
Browse by: Latest US Patents, China's latest patents, Technical Efficacy Thesaurus, Application Domain, Technology Topic.
© 2024 PatSnap. All rights reserved.Legal|Privacy policy|Modern Slavery Act Transparency Statement|Sitemap