Microhole drilling system based on start-stop technology
A drilling and micro-hole technology, applied in the direction of boring/drilling, drilling/drilling equipment, large fixed members, etc., can solve the problem of inability to accurately control the hole depth, not suitable for metal parts cutting, low processing efficiency, etc. problems, achieve the effect of reducing labor intensity and technical requirements of workers, eliminating cutting chatter, and improving processing efficiency
- Summary
- Abstract
- Description
- Claims
- Application Information
AI Technical Summary
Problems solved by technology
Method used
Image
Examples
Example Embodiment
[0047] Example 1, see attached figure 1 ~ Attached Figure 8 , A micro-hole drilling system based on start-stop technology, including a base 9, a column fixed to the base 9, a support 3 fixed to the column 1, a drilling mechanism set on the support 3, The air cushion mechanism on the base 9, the three-way pressure sensor 6, the single-chip computer 19, and the distance measuring mechanism.
[0048] The drilling mechanism includes a vertical support shaft 20 movably set on the support 3, a rocker arm 16 set on the support shaft 20, a connecting plate 2 fixed on the support shaft 20, and a vertical support shaft fixed on the connecting plate 2. The electric spindle 4 passes through the support 3, and a chuck 5 is provided at the lower end of the electric spindle 4.
[0049] The air-cushion mechanism is located directly below the electric spindle 4. The air-cushion mechanism includes an air-cushion plate 8 on the base 9, a support plate 7 fixed to the upper end surface of the air-cushio
PUM
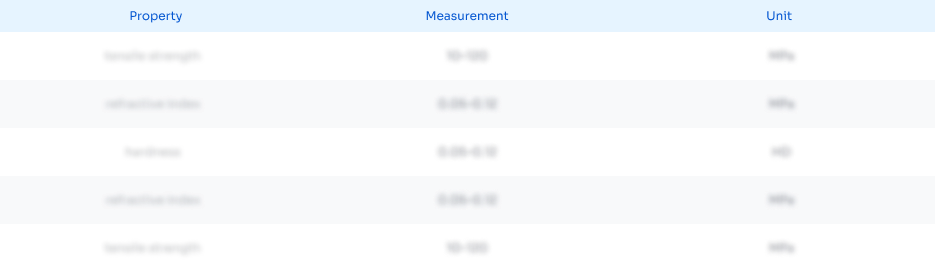
Abstract
Description
Claims
Application Information
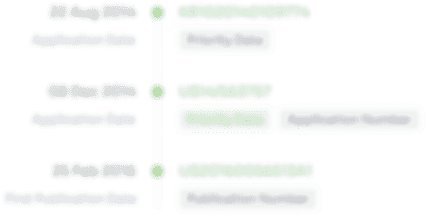
- R&D Engineer
- R&D Manager
- IP Professional
- Industry Leading Data Capabilities
- Powerful AI technology
- Patent DNA Extraction
Browse by: Latest US Patents, China's latest patents, Technical Efficacy Thesaurus, Application Domain, Technology Topic.
© 2024 PatSnap. All rights reserved.Legal|Privacy policy|Modern Slavery Act Transparency Statement|Sitemap