Low-cost high-strength steel plate for engineering machinery, and production method thereof
A technology for construction machinery and production methods, which is applied in the field of low-cost and high-strength construction machinery steel plates and their production, can solve problems such as affecting the production profits of enterprises and high production costs, achieve excellent comprehensive mechanical properties, and solve the problem of coarse grains. Uneven, low production cost effect
- Summary
- Abstract
- Description
- Claims
- Application Information
AI Technical Summary
Benefits of technology
Problems solved by technology
Method used
Examples
Embodiment 1
[0029] Embodiment 1: The composition ratio and production process of the low-cost high-strength steel plate for construction machinery are as follows.
[0030] The mass percentage of the chemical composition of the steel plate is: C 0.17%, Si 0.3%, Mn 1.3%, P 0.007%, S 0.004%, Ni 0.6%, Cr 0.5%, Nb 0.03%, Al 0.02%, Mo 0.40%, Ti 0.028%, B 0.003%, the balance is Fe and unavoidable impurities; the thickness of the steel plate is 80mm.
[0031] The processing step of this steel plate production method is as follows:
[0032] (1) Smelting process: the molten steel is smelted in a vacuum induction furnace first, and the order of adding aluminum-titanium-boron alloy elements is as follows: first add aluminum for deoxidation, then add titanium to fix nitrogen, and add boron before the molten steel is released to ensure that the molten steel contains 0.003% boron content.
[0033] (2) Casting process, casting molten steel after smelting into a billet (steel billet) at a casting temperatu
Embodiment 2
[0038] Embodiment 2: The composition ratio and production process of the low-cost high-strength steel plate for construction machinery are as follows.
[0039] The mass percentage of the chemical composition of the steel plate is: C 0.16%, Si 0.35%, Mn 1.4%, P 0.009%, S 0.005%, Ni 0.4%, Cr 0.4%, Nb 0.02%, Al 0.06%, Mo 0.37%, Ti 0.016%, B 0.0022%, the balance is Fe and unavoidable impurities; the thickness of the steel plate is 80mm.
[0040] The processing step of this steel plate production method is as follows:
[0041] (1) Smelting process: the molten steel is smelted in a vacuum induction furnace first, and the order of adding aluminum-titanium-boron alloy elements is as follows: first add aluminum for deoxidation, then add titanium to fix nitrogen, and add boron before the molten steel is released to ensure that the molten steel contains 0.0022% boron content.
[0042] (2) Casting process, casting molten steel after smelting into a billet (steel billet) at a casting temper
Embodiment 3
[0047] Embodiment 3: The composition ratio and production process of the low-cost high-strength steel plate for construction machinery are as follows.
[0048] The mass percentage of the chemical composition of the steel plate is: C 0.18%, Si 0.37%, Mn 1.0%, P 0.012%, S 0.009%, Ni 0.5%, Cr 0.3%, Nb 0.02%, Al 0.04%, Mo 0.34%, Ti 0.010%, B 0.0016%, the balance is Fe and unavoidable impurities; the thickness of the steel plate is 80mm.
[0049] The processing step of this steel plate production method is as follows:
[0050] (1) Smelting process: the molten steel is smelted in a vacuum induction furnace first, and the order of adding aluminum-titanium-boron alloy elements is as follows: first add aluminum for deoxidation, then add titanium to fix nitrogen, and add boron before the molten steel is released to ensure that the molten steel contains 0.0016% boron content.
[0051] (2) Casting process, casting molten steel after smelting into a billet (steel billet) at a casting temper
PUM
Property | Measurement | Unit |
---|---|---|
Thickness | aaaaa | aaaaa |
Yield strength | aaaaa | aaaaa |
Tensile strength | aaaaa | aaaaa |
Abstract
Description
Claims
Application Information
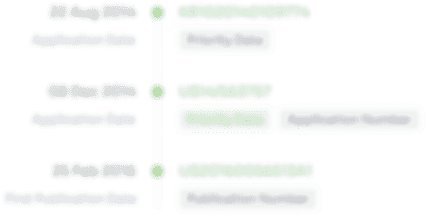
- R&D Engineer
- R&D Manager
- IP Professional
- Industry Leading Data Capabilities
- Powerful AI technology
- Patent DNA Extraction
Browse by: Latest US Patents, China's latest patents, Technical Efficacy Thesaurus, Application Domain, Technology Topic.
© 2024 PatSnap. All rights reserved.Legal|Privacy policy|Modern Slavery Act Transparency Statement|Sitemap