Automobile trim material combined with non-woven fabric and woven fabric
A technology of automotive interior and woven fabrics, applied in the field of automotive interior materials, can solve the problems of polluting the human respiratory system and skin, environmental pollution of waste materials, and poor rigidity of PU boards, etc., to achieve convenient operation and management, short process flow, Strong tensile effect
- Summary
- Abstract
- Description
- Claims
- Application Information
AI Technical Summary
Benefits of technology
Problems solved by technology
Method used
Examples
Embodiment 1
[0025] Step 1. Cut the natural fibers into short fibers of 50mm, put them in a stainless steel container and mix them with sodium bicarbonate solution and stir for 60 minutes. Mix 10% by weight with water to form a solution;
[0026] Step 2. Wash the hemp fiber with clean water to remove the sodium bicarbonate solution in the natural fiber, then put it in a constant temperature bath in warm water at 20°C for 60 minutes, remove the residual sodium bicarbonate in the fiber solution, and then vacuum dry it;
[0027] Step 3, adding 0.5% styrene monomer and 0.8% cerium ammonium nitrate by weight to the dried natural fibers, performing a chemical reaction, washing with clear water, and then drying;
[0028] Step 4, put the dried natural fibers on the wool machine equipment and open and mix with polypropylene fibers to obtain mixed fibers. The proportion of natural fibers and polypropylene fibers is distributed by weight: 50% of natural fibers, 50% of polypropylene fibers 30%;
[0029
Embodiment 2
[0038] Step 1. Cut the natural fibers into short fibers of 60 mm, put them in a stainless steel container and mix them with sodium bicarbonate solution and stir for 70 minutes. Mix with clear water by 15% by weight to form a solution;
[0039] Step 2. Wash the hemp fiber with clean water to remove the sodium bicarbonate solution in the natural fiber, then put it in a constant temperature bath in warm water at 25°C for 70 minutes, remove the residual sodium bicarbonate in the fiber solution, and then vacuum dry it;
[0040] Step 3, adding 1% by weight of styrene monomer and 0.1% cerium ammonium nitrate to the dried natural fibers, performing a chemical reaction, washing with clear water, and then drying;
[0041] Step 4. Put the dried natural fibers on the wool machine equipment and open and mix with polypropylene fibers to obtain mixed fibers. The proportioning ratio of natural fibers and polypropylene fibers is as follows: natural fibers 60%, polypropylene fibers 40%;
[0042]
Embodiment 3
[0051] Step 1. Cut the natural fibers into short fibers of 70 mm, put them in a stainless steel container and mix them with sodium bicarbonate solution and stir for 80 minutes. Mix with clear water by 20% by weight to form a solution;
[0052] Step 2. Wash the hemp fiber with clean water to remove the sodium bicarbonate solution in the natural fiber, then put it in a constant temperature bath in warm water at 30°C for 80 minutes, remove the residual sodium bicarbonate in the fiber solution, and then vacuum dry it;
[0053] Step 3, adding 1.2% styrene monomer and 0.12% cerium ammonium nitrate by weight to the dried natural fibers, performing a chemical reaction, washing with clear water, and then drying;
[0054] Step 4, put the dried natural fiber on the wool machine equipment and open and mix with polypropylene fiber to obtain mixed fiber. The proportion of natural fiber and polypropylene fiber is divided by weight: natural fiber 70%, polypropylene fiber 50%;
[0055] Step 5,
PUM
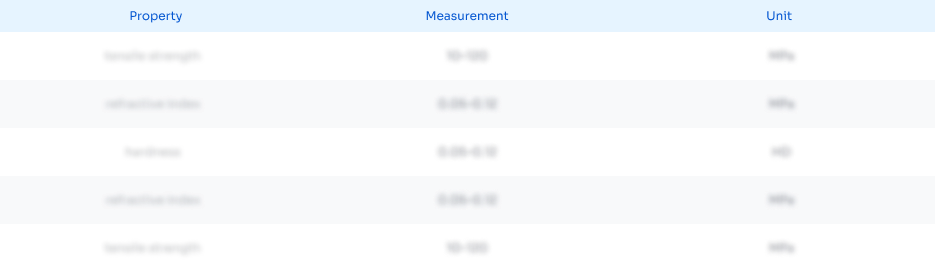
Abstract
Description
Claims
Application Information
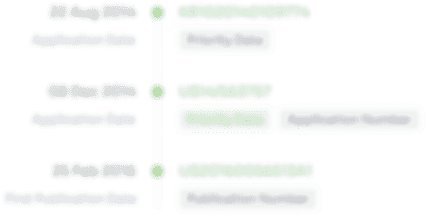
- R&D Engineer
- R&D Manager
- IP Professional
- Industry Leading Data Capabilities
- Powerful AI technology
- Patent DNA Extraction
Browse by: Latest US Patents, China's latest patents, Technical Efficacy Thesaurus, Application Domain, Technology Topic.
© 2024 PatSnap. All rights reserved.Legal|Privacy policy|Modern Slavery Act Transparency Statement|Sitemap