Preparation method of ultrasonic-dispersion tungsten carbide and silicon carbide-carbon fiber friction material
A technology of tungsten carbide, silicon carbide and friction materials, which is applied in the field of preparation of friction materials, can solve the problems of reduced friction performance and potential safety hazards, and achieve the effect of improving wear resistance and high manufacturing cost
- Summary
- Abstract
- Description
- Claims
- Application Information
AI Technical Summary
Benefits of technology
Problems solved by technology
Method used
Examples
Embodiment 1
[0019] (1) Set the density to 1.8g / cm 3 The graphitized carbon fiber blanket is fed with a mixed gas of propane gas and nitrogen at a temperature of 900°C. The molar ratio of propane gas: nitrogen is 1:4, the flow rate is controlled at 50ml / min, and the carburizing treatment is performed for 24 hours to obtain a carburized carbon fiber blanket. ;
[0020] (2) Immerse the above-mentioned carburized carbon fiber blanket into a slurry with a particle size of less than 0.3 μm and a content of 5% tungsten carbide, place it in an ultrasonic cleaner and fill it with tungsten carbide for 50 minutes, take it out and dry it to obtain a filled tungsten carbide carbon fiber blanket, slurry The material is an aqueous solution containing 1.5% ammonium polyacrylate with a pH value of 9;
[0021] (3) Pass the above-mentioned filled tungsten carbide carbon fiber blanket into a mixed gas of trichloromethylsilane gas, hydrogen gas and argon gas at a temperature of 900 °C, and the molar ratio o
Embodiment 2
[0025] (1) Set the density to 0.8g / cm 3 The graphitized carbon fiber blanket is fed with a mixture of propane gas and nitrogen at a temperature of 1000°C. The molar ratio of propane gas: nitrogen is 1:5, the flow rate is controlled at 350ml / min, and the carburizing treatment is performed for 18 hours to obtain a carburized carbon fiber blanket. ;
[0026] (2) Immerse the above carburized carbon fiber blanket into a slurry with a particle size of less than 0.3 μm and a content of 12% tungsten carbide, place it in an ultrasonic cleaner and fill it with tungsten carbide for 40 minutes, take it out and dry it to obtain a filled tungsten carbide carbon fiber blanket, slurry The material is an aqueous solution containing 1% ammonium polyacrylate with a pH value of 10;
[0027] (3) Pass the above-mentioned filled tungsten carbide carbon fiber blanket into a mixed gas of trichloromethylsilane gas, hydrogen gas and argon gas at a temperature of 1000 ° C. The molar ratio of trichlorom
Embodiment 3
[0031] (1) Set the density to 0.1g / cm 3 The graphitized carbon fiber blanket is fed with a mixed gas of propane gas and nitrogen at a temperature of 1100°C. The molar ratio of propane gas: nitrogen is 1:6, the flow rate is controlled at 600ml / min, and the carburizing treatment is performed for 10 hours to obtain a carburized carbon fiber blanket. ;
[0032] (2) Immerse the above carburized carbon fiber blanket into a slurry with a particle size of less than 0.3 μm and a content of 20% tungsten carbide, place it in an ultrasonic cleaner and fill it with tungsten carbide for 30 minutes, take it out and dry it to obtain a filled tungsten carbide carbon fiber blanket, slurry The material is an aqueous solution containing 0.5% ammonium polyacrylate with a pH value of 11;
[0033] (3) Pass the above-mentioned filled tungsten carbide carbon fiber blanket into a mixed gas of trichloromethylsilane gas, hydrogen gas and argon gas at a temperature of 1100 °C, and the molar ratio of tri
PUM
Property | Measurement | Unit |
---|---|---|
Diameter | aaaaa | aaaaa |
Abstract
Description
Claims
Application Information
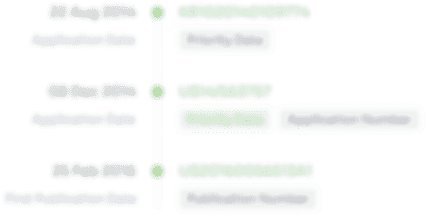
- R&D Engineer
- R&D Manager
- IP Professional
- Industry Leading Data Capabilities
- Powerful AI technology
- Patent DNA Extraction
Browse by: Latest US Patents, China's latest patents, Technical Efficacy Thesaurus, Application Domain, Technology Topic.
© 2024 PatSnap. All rights reserved.Legal|Privacy policy|Modern Slavery Act Transparency Statement|Sitemap