Cold spinning device used for steel seamless gas cylinder
A seamless gas cylinder and cold spinning technology, which is applied in the field of gas cylinder cold spinning processing equipment, can solve problems such as uneven force on the spinning wheel, and achieve the effect of eliminating surface wavy lines, good stability, and eliminating wavy lines
- Summary
- Abstract
- Description
- Claims
- Application Information
AI Technical Summary
Benefits of technology
Problems solved by technology
Method used
Image
Examples
Embodiment Construction
[0037] Such as Figure 3-6 As shown, a cold spinning device for steel seamless gas cylinders includes a mandrel 1 that extends into the preform to process the inner surface, a connecting assembly connected to the end of the mandrel 1, and a preform located outside the preform. Wheel assembly.
[0038] Such as image 3 and Figure 4 As shown, the rotary wheel assembly includes a rotary wheel bracket 12, a spinning shaft 11 rotatably fitted on the rotary wheel bracket 12, and a rotary wheel 14 sleeved on the spinning shaft 11 and pressed against the outer surface of the preform.
[0039] One end of the spinning shaft 11 stretches into the fixed wheel casing 13 with the wheel bracket 12, and the other end 19 stretches into the supporting overcoat 16 fixed with the spinning wheel bracket 12, and the spinning shaft 11 end in the supporting overcoat 16 is also The sleeve is provided with a support lining 18, and a double row of 6314 bearings 17 is provided between the support lining
PUM
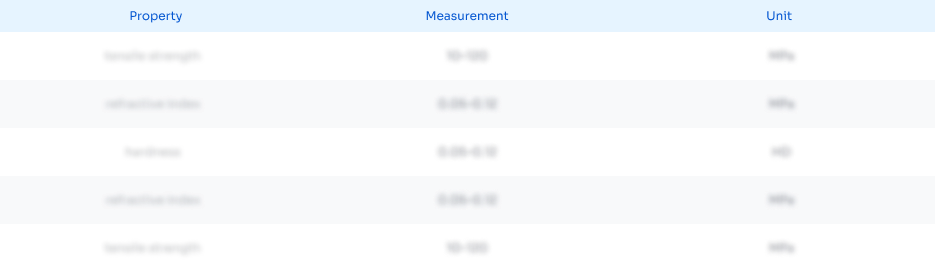
Abstract
Description
Claims
Application Information
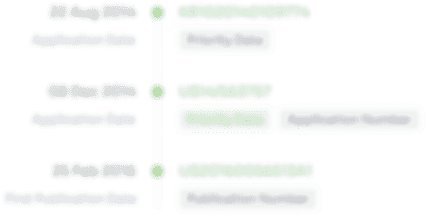
- R&D Engineer
- R&D Manager
- IP Professional
- Industry Leading Data Capabilities
- Powerful AI technology
- Patent DNA Extraction
Browse by: Latest US Patents, China's latest patents, Technical Efficacy Thesaurus, Application Domain, Technology Topic.
© 2024 PatSnap. All rights reserved.Legal|Privacy policy|Modern Slavery Act Transparency Statement|Sitemap