Full-automatic welding machine
A fully automatic welding and welding device technology, applied in welding equipment, auxiliary welding equipment, welding/cutting auxiliary equipment, etc., can solve the problem of low welding efficiency, inaccurate feeding and unloading methods of tubular materials, and inability to achieve welding density precise control, etc.
- Summary
- Abstract
- Description
- Claims
- Application Information
AI Technical Summary
Benefits of technology
Problems solved by technology
Method used
Image
Examples
Embodiment Construction
[0039] Below in conjunction with accompanying drawing and embodiment of description, specific embodiment of the present invention is described in further detail:
[0040] refer to Figure 1 to Figure 23 A kind of fully automatic welding machine shown, comprises feeding device 1, welding fittings feeding device 2, welding device 3, unloading device 4 and circular turntable 5, described feeding device 1, welding fittings feeding device 2. The welding device 3 and the feeding device 4 are both arranged on the side of the turntable 5, and the top edge of the turntable 5 is provided with a plurality of placement rods 5b for the materials to be sleeved. The feeding device 1 includes a feeding device 1a, an arrangement device 1b and a first rotating device 1c, the feeding device 1a includes a discharge port, the arrangement device 1b is provided with an arrangement track 1b1 matched with the discharge port, and the first rotation The device 1c is provided with a first transition bar 1c
PUM
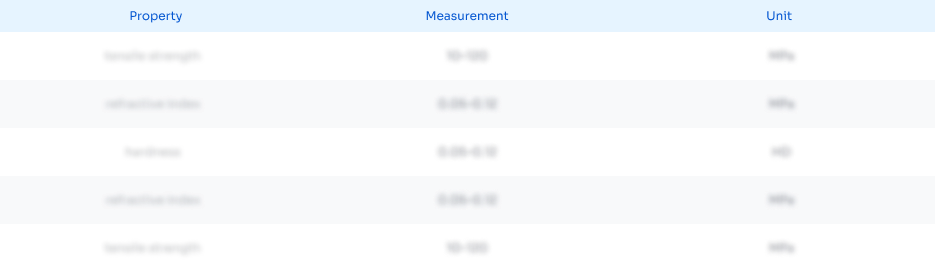
Abstract
Description
Claims
Application Information
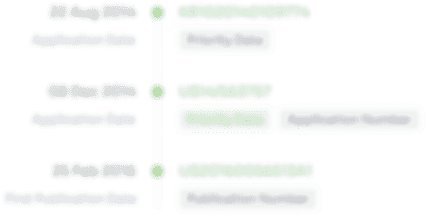
- R&D Engineer
- R&D Manager
- IP Professional
- Industry Leading Data Capabilities
- Powerful AI technology
- Patent DNA Extraction
Browse by: Latest US Patents, China's latest patents, Technical Efficacy Thesaurus, Application Domain, Technology Topic.
© 2024 PatSnap. All rights reserved.Legal|Privacy policy|Modern Slavery Act Transparency Statement|Sitemap