Composite reverse osmosis membrane with high temperature resistance and high flux as well as preparation method thereof
A reverse osmosis membrane, high-flux technology, applied in the direction of reverse osmosis, semi-permeable membrane separation, chemical instruments and methods, etc., can solve the problems of low efficiency, poor high temperature resistance, short life of reverse osmosis membrane, etc., to avoid biological Effects of pollution, increased service life, improved thermal stability and solubility properties
- Summary
- Abstract
- Description
- Claims
- Application Information
AI Technical Summary
Problems solved by technology
Method used
Image
Examples
Embodiment 1
[0025] To prepare a composite reverse osmosis membrane containing 17% fluorine-containing polyaryl ether ketone and a base membrane doped with 0.02% graphene oxide, the specific steps are as follows:
[0026] A. Prepare trifluoromethyl polyaryl ether ketone, DMF (dimethylformamide), polyvinylpyrrolidone and graphene oxide powder according to the weight ratio of 17:68.98:14:0.02 to form a casting solution, stir evenly, and let stand still Ultrasonic degassing for 10 minutes after 1 hour, as the support layer casting liquid;
[0027] B. Apply the casting liquid prepared in step A to the non-woven fabric with a film scraper with a thickness of 80μm, then evaporate at room temperature for 10s and then immerse in 20℃ deionized water to gel and solidify into a film, and then place it in a 60℃ oven Dry for 6 hours to obtain a support layer;
[0028] C. Separately configure solution A: the solute is m-diphenylamine, the solvent is water, and the concentration is 6%wt; the configuration solutio
Embodiment 2
[0033] To prepare a composite reverse osmosis membrane containing 18% fluorine-containing polyaryl ether ketone, and the base membrane doped with 0.05% graphene oxide, the specific steps are as follows:
[0034] A. Prepare the fluorine-containing polyaryl ether ketone, DMAc (dimethylacetamide), polyethylene glycol and graphene oxide powder into a casting liquid according to the ratio of 18:69.95:12:0.05, stir it evenly, and let it stand for 1h before ultrasonic Degas for 15 minutes, as the support layer casting liquid; the fluorine-containing polyaryl ether ketone is p-bisphenol and 1,4-bis(4'-fluorobenzoyl)benzene and 1,3-bis(4'-fluorobenzene) Acyl) benzene polymer PPAEK-AF.
[0035] B. Apply the casting liquid prepared in step A to the non-woven fabric with a film scraper with a thickness of 100μm, then evaporate at room temperature for 10s and then immerse in 25℃ deionized water to gel and solidify into a film, and then place it in a 60℃ oven Dry for 5 hours to obtain a support la
Embodiment 3
[0041] To prepare a composite reverse osmosis membrane containing 19% fluorine-containing polyaryl ether ketone, the base membrane is doped with 0.05% graphene oxide, and the desalination layer is doped with graphene oxide. The specific steps are as follows:
[0042] A. Prepare fluorine-containing polyaryl ether ketone, DMAc (dimethylacetamide), polyethylene glycol and graphene oxide powder into a casting liquid according to the ratio 19:69.98:11:0.05, stir it evenly, and let it stand for 1h before ultrasonic Degas for 15 minutes as a support layer casting solution; among them, the fluorine-containing polyaryl ether ketone is m-bisphenol, 1,4-bis(4'-fluorobenzoyl)benzene and 1,3-bis(4'-fluorobenzene) Acyl) benzene polymer MPAEK-AF.
[0043] B. Apply the casting liquid prepared in step A to the non-woven fabric with a film scraping machine with a thickness of 120μm, then evaporate at room temperature for 10s and then immerse in 20℃ deionized water to gel and solidify into a film, and t
PUM
Property | Measurement | Unit |
---|---|---|
Thickness | aaaaa | aaaaa |
Thickness | aaaaa | aaaaa |
Average pore size | aaaaa | aaaaa |
Abstract
Description
Claims
Application Information
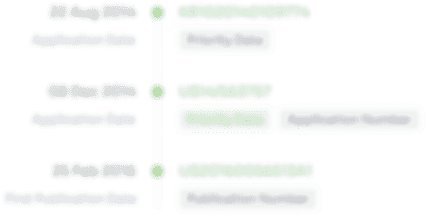
- R&D Engineer
- R&D Manager
- IP Professional
- Industry Leading Data Capabilities
- Powerful AI technology
- Patent DNA Extraction
Browse by: Latest US Patents, China's latest patents, Technical Efficacy Thesaurus, Application Domain, Technology Topic.
© 2024 PatSnap. All rights reserved.Legal|Privacy policy|Modern Slavery Act Transparency Statement|Sitemap