Putty powder and preparation method thereof
A technology for putty powder and powdery materials, applied in the direction of filling slurry, etc., can solve the problems of easy leakage, poor workability, easy to produce cracks, etc., and achieve the effects of improving environmental pollution, reducing production costs, and good fluidity.
- Summary
- Abstract
- Description
- Claims
- Application Information
AI Technical Summary
Problems solved by technology
Method used
Examples
Example Embodiment
[0048] Another embodiment of the present invention also provides a method for preparing the putty powder described in the above embodiment, including the following steps:
[0049] Step 1: Preparation of powdery materials: take the Yellow River silt, dry fine sand and silt, and transport them to the feeder and pulverizer in turn, then put them in the dryer for drying, and then sieving to obtain 200-300 mesh powdered materials;
[0050] Step 2: Preparation of rosin saponification: Put rosin, sodium hydroxide and water into the reaction kettle and heat at 160~190℃ for 20~40min to obtain a brown transparent paste. Put the paste into a vacuum of 93.3~98.6KPa. After drying in a vacuum oven at a temperature of 60-80°C for 5-7 hours, saponified rosin is obtained by crushing;
[0051] Step 3: Preparation of putty powder: take cement and the powdered material obtained in step one into the putty powder mixer, stir in a dry state for 1 to 2 minutes, then add active diluent, epoxy resin, redispersib
Example Embodiment
[0055] Example 1: A putty powder comprising the following raw material components in parts by weight: 25 parts of Yellow River silt, 35 parts of dry fine sand, 10 parts of silt, 20 parts of cement, 5 parts of active diluent, 20 parts of emulsifier, 3 parts of epoxy resin, 0.5 parts of vinyl acetate-ethylene copolymer emulsion, 10 parts of rosin saponification, 1 part of antifreeze, 8 parts of anti-cracking agent, 5 parts of water retention agent And 8 parts of film former.
[0056] The reactive diluent includes 5 parts by weight of butyl glycidyl ether and 7 parts by weight of ethylene glycol diglycidyl ether; the emulsifier includes a nonionic ratio of 3:1 by weight. Emulsifier and cationic emulsifier; the nonionic emulsifier is cetyl polyoxyethylene ether;
[0057] The cationic emulsifier is octadecyl trimethyl ammonium chloride, cetyl trimethyl ammonium chloride, octadecyl dimethyl benzyl ammonium chloride and cetyl pyridinium cation ammonium chloride mixture;
[0058] Said rosin
Example Embodiment
[0073] Example 2: A putty powder, including the following raw material components in parts by weight: 25 to 38 parts of Yellow River silt, 35 parts of Yellow River silt, 30 parts of dry fine sand, 22 parts of silt, 16 parts of silt Cement, 8 parts of reactive diluent, 12 parts of emulsifier, 7 parts of epoxy resin, 6 parts of rosin saponification, 1 part of vinyl acetate-ethylene copolymer emulsion, 3 parts of antifreeze, 5 parts of Anti-cracking agent, 10 parts of water retention agent and 6 parts of film-forming agent.
[0074] The reactive diluent includes 8 parts by weight of butyl glycidyl ether and 4 parts by weight of ethylene glycol diglycidyl ether; the emulsifier includes a nonionic ratio of 3:1 by weight. Emulsifier and cationic emulsifier; the non-ionic emulsifier is nonylphenol polyoxyethylene ether, fatty alcohol polyoxyethylene ether, cetyl polyoxyethylene ether, abietic acid polyoxyethylene ether or lauric acid polyoxyethylene ether mixture;
[0075] The cationic emu
PUM
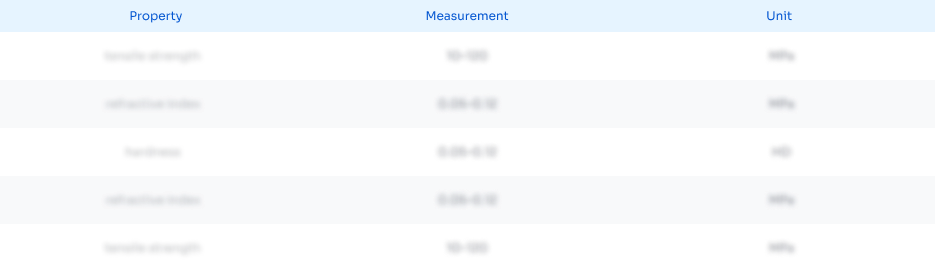
Abstract
Description
Claims
Application Information
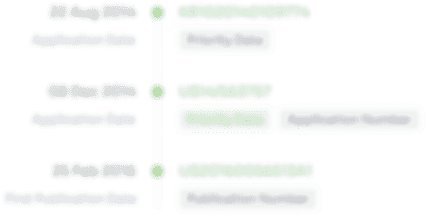
- R&D Engineer
- R&D Manager
- IP Professional
- Industry Leading Data Capabilities
- Powerful AI technology
- Patent DNA Extraction
Browse by: Latest US Patents, China's latest patents, Technical Efficacy Thesaurus, Application Domain, Technology Topic.
© 2024 PatSnap. All rights reserved.Legal|Privacy policy|Modern Slavery Act Transparency Statement|Sitemap