A mold for producing cylinder liners of twin-screw extruders
A technology of twin-screw extrusion and molding machine, applied in the direction of manufacturing tools, casting molding equipment, casting mold components, etc., to achieve the effects of convenient recycling, reducing white mouth, and improving feeding efficiency
- Summary
- Abstract
- Description
- Claims
- Application Information
AI Technical Summary
Benefits of technology
Problems solved by technology
Method used
Image
Examples
Embodiment 1
[0041] Such as figure 1 , figure 2 , image 3 , Figure 4 , Figure 5 with Image 6 As shown, a mold for producing a twin-screw extruder barrel bushing of this embodiment includes an upper box and a lower box. The upper box and the lower box enclose a twin-screw The molding cavity 11 of the barrel bushing of the extruder; the inner wall of the molding cavity 11 is ∞-shaped, and the sharp corners of the ∞-shaped junction form a thick triangular area; the middle of the molding cavity 11 is provided with a twin screw mounting hole Molded mud core 9; the top middle of the molding cavity 11 in the upper box body is provided with a heating riser 7; the bottom middle of the molding cavity 11 in the lower box body is provided with a graphite chilled iron 8; the molding cavity 11 side is close to the front and rear ends The inner gate 6 is symmetrically arranged at the part, and the outer gate 1 communicating with the inner gate 6 and a pouring channel are simultaneously arranged on the up
Embodiment 2
[0045] Such as figure 2 , image 3 , Figure 4 , Figure 5 with Image 6 As shown, the mold for producing the barrel bushing of the twin-screw extruder in this embodiment, the pouring channel is a side-mounted pouring channel, and includes a straight runner 2 and a straight runner provided in the middle of one side of the molding cavity 11. The sprue 3, the runner 4, the common riser 5 and the inner gate 6, the bottom of the sprue 2 is provided with a sprue socket 3 with an arc bottom; the upper part of the sprue socket 3 Both sides are connected to the horizontal runner 4; the ends of the two runners 4 are respectively connected with a common side riser 5; the two common side risers 5 are respectively connected with two inner gates 6; Two ingates 6 are connected with the molding cavity 11. The sprue socket 3 and the runner 4 are covered with a filter screen, and the filter screen extends into the common side riser 5 to play a filtering role.
[0046] In this embodiment, the molte
Embodiment 3
[0048] Such as figure 1 with figure 2 As shown in the present embodiment, in a mold for producing a barrel bushing of a twin-screw extruder, the sprue 2 is a vertical cylindrical hollow pipe, and the sprue 2 is located in the upper box, and The runner 2 is arranged perpendicular to the molding cavity 11, and the bottom of the sprue 2 is located on the parting surface of the upper box; the molten metal inlet end of the sprue 2 is provided with a funnel-shaped outer gate 1.
[0049] In this embodiment, the molten metal is poured from the funnel-shaped outer gate 1, passes through the sprue 2 and flows into the sprue socket 3. The funnel-shaped outer gate 1 receives the molten metal from the ladle, prevents splashing and overflow, facilitates pouring, and reduces the direct impact of the molten metal on the sprue 2;
PUM
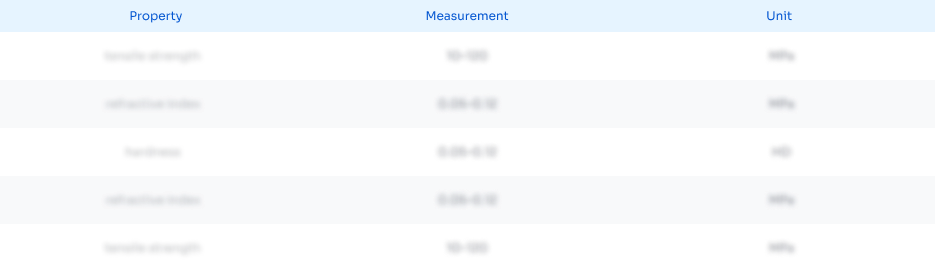
Abstract
Description
Claims
Application Information
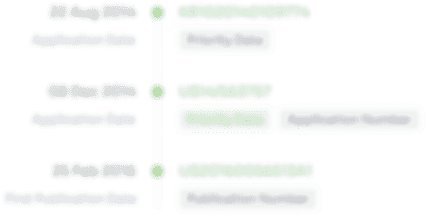
- R&D Engineer
- R&D Manager
- IP Professional
- Industry Leading Data Capabilities
- Powerful AI technology
- Patent DNA Extraction
Browse by: Latest US Patents, China's latest patents, Technical Efficacy Thesaurus, Application Domain, Technology Topic.
© 2024 PatSnap. All rights reserved.Legal|Privacy policy|Modern Slavery Act Transparency Statement|Sitemap