Method for manufacturing sturdy and durable side stand
A manufacturing method and technology of side brackets, applied to bicycle brackets, bicycle accessories, fireproof coatings, etc., can solve problems affecting the strength and service life of side brackets, corrosion of side brackets, damage and drop of coating surfaces of side brackets, etc. To achieve improved robustness, long service life, and hard texture
- Summary
- Abstract
- Description
- Claims
- Application Information
AI Technical Summary
Benefits of technology
Problems solved by technology
Method used
Examples
Embodiment 1
[0021] A method for manufacturing a strong and durable side bracket, comprising the following steps:
[0022] S1. Billet processing, put the alloy steel block into the smelting furnace for smelting. After the smelting is completed, put the obtained billet into the continuous casting machine for casting to obtain the billet. The temperature of the smelting furnace is 600°C;
[0023] S2. Blank treatment. Put the blank processed in S1 into the annealing furnace and process it through the continuous annealing process, which is used to release the stress of the blank. The continuous annealing adopts a temperature of 720°C, heats it for 95s, and heats it at 5°C / s Speed jet cooling to 600°C, then jet cooling to 110°C at a cooling rate of 46°C / s, then heating to 300°C and tempering for 120s;
[0024] S3, cutting the blank, placing the blank after the annealing in S2 on the cutting machine, and dividing the blank into multiple workpieces;
[0025] S4, the workpiece is polished, and
Embodiment 2
[0031] A method for manufacturing a strong and durable side bracket, comprising the following steps:
[0032] S1. Billet processing, put the alloy steel block into the smelting furnace for smelting. After the smelting is completed, put the obtained billet into the continuous casting machine for casting to obtain the billet. The temperature of the smelting furnace is 690°C;
[0033] S2. Blank treatment, put the blank processed in S1 into the annealing furnace and process it through continuous annealing process, which is used to release the stress of the blank. The continuous annealing adopts a temperature of 742°C and heats it for 100s, and heats it at 6°C / s Speed jet cooling to 620°C, then jet cooling to 120°C at a cooling rate of 49°C / s, then heating to 320°C and tempering for 135s;
[0034] S3, cutting the blank, placing the blank after the annealing in S2 on the cutting machine, and dividing the blank into multiple workpieces;
[0035] S4, the workpiece is polished, and
Embodiment 3
[0041] A method for manufacturing a strong and durable side bracket, comprising the following steps:
[0042] S1. Billet processing, put the alloy steel block into the smelting furnace for smelting. After the smelting is completed, put the obtained billet into the continuous casting machine for casting to obtain the billet. The temperature of the smelting furnace is 750°C;
[0043] S2. Blank treatment, put the blank processed in S1 into the annealing furnace and process it through continuous annealing process, which is used to release the stress of the blank. The continuous annealing temperature is 776°C and the heat preservation is 112°C, and the temperature is 7.6°C / s Speed jet cooling to 665°C, then jet cooling to 170°C at a cooling rate of 51°C / s, and then heating to 365°C and tempering for 160s;
[0044] S3, cutting the blank, placing the blank after the annealing in S2 on the cutting machine, and dividing the blank into multiple workpieces;
[0045] S4, the workpiece
PUM
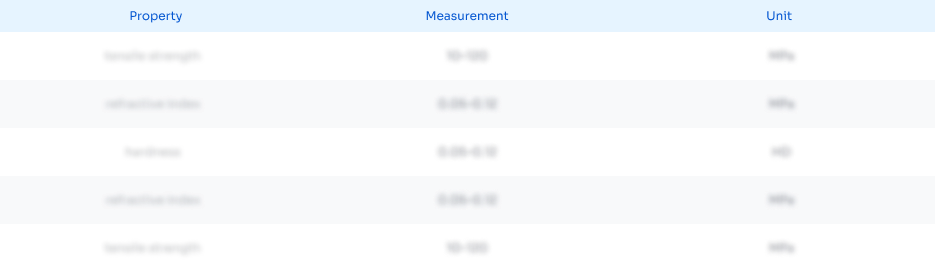
Abstract
Description
Claims
Application Information
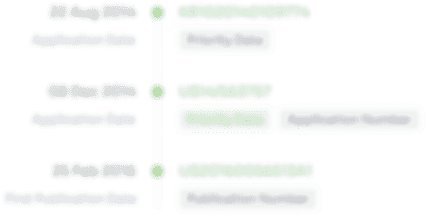
- R&D Engineer
- R&D Manager
- IP Professional
- Industry Leading Data Capabilities
- Powerful AI technology
- Patent DNA Extraction
Browse by: Latest US Patents, China's latest patents, Technical Efficacy Thesaurus, Application Domain, Technology Topic.
© 2024 PatSnap. All rights reserved.Legal|Privacy policy|Modern Slavery Act Transparency Statement|Sitemap