Fireproof and thermal-insulation composite for building
A technology of fire-proof thermal insulation and composite materials, which is applied in the field of fire-proof thermal insulation composite materials for buildings, can solve the problems of poor fire performance, reduced strength, and affect the overall performance, etc., so as to improve the fire retardant performance, improve the crack resistance, and improve the fire rating. Effect
- Summary
- Abstract
- Description
- Claims
- Application Information
AI Technical Summary
Problems solved by technology
Method used
Image
Examples
Embodiment 1
[0017] A fireproof and thermal insulation composite material for buildings, which is made of the following components in parts by weight: 150-160 parts of sulphoaluminate cement, 70-80 parts of high-density polyethylene, 60-70 parts of fly ash, and 45-50 parts of gypsum 30-40 parts of hollow microspheres, 20-25 parts of basalt fiber, 8-10 parts of sodium aluminate, 7-10 parts of anhydrous sodium sulfate, 4-6 parts of silicon dioxide, 3-5 parts of magnesium oxide, hydrogen 2-4 parts of calcium oxide, 2-3 parts of lithium carbonate, 1.5-2.0 parts of silicone water repellent, 1.0-1.5 parts of vinyl dimethyl siloxane, γ-aminopropyl triethoxysilane coupling agent 0.5-0.8 parts, 3.5-4.0 parts of paraffin, 25-30 parts of absolute ethanol, 100-110 parts of water, the preparation method comprises the following steps:
[0018] (1) Mix absolute ethanol and water at a mass ratio of 8-9:1, heat to 60-70°C, add γ-aminopropyltriethoxysilane coupling agent under stirring, and stir for 10-15 minu
Embodiment 2
[0025] A fireproof and thermal insulation composite material for buildings, which is made of the following components in parts by weight: 150-160 parts of sulphoaluminate cement, 70-80 parts of high-density polyethylene, 60-70 parts of fly ash, and 45-50 parts of gypsum 30-40 parts of hollow microspheres, 20-25 parts of basalt fiber, 8-10 parts of sodium aluminate, 7-10 parts of anhydrous sodium sulfate, 4-6 parts of silicon dioxide, 3-5 parts of magnesium oxide, hydrogen 2-4 parts of calcium oxide, 2-3 parts of lithium carbonate, 1.5-2.0 parts of silicone water repellent, 1.0-1.5 parts of vinyl dimethyl siloxane, γ-aminopropyl triethoxysilane coupling agent 0.5-0.8 parts, 3.5-4.0 parts of paraffin, 25-30 parts of absolute ethanol, 100-110 parts of water, the preparation method comprises the following steps:
[0026] (1) Mix absolute ethanol and water at a mass ratio of 8-9:1, heat to 60-70°C, add γ-aminopropyltriethoxysilane coupling agent under stirring, and stir for 10-15 minu
Embodiment 3
[0033] A fireproof and thermal insulation composite material for buildings, which is made of the following components in parts by weight: 150-160 parts of sulphoaluminate cement, 70-80 parts of high-density polyethylene, 60-70 parts of fly ash, and 45-50 parts of gypsum 30-40 parts of hollow microspheres, 20-25 parts of basalt fiber, 8-10 parts of sodium aluminate, 7-10 parts of anhydrous sodium sulfate, 4-6 parts of silicon dioxide, 3-5 parts of magnesium oxide, hydrogen 2-4 parts of calcium oxide, 2-3 parts of lithium carbonate, 1.5-2.0 parts of silicone water repellent, 1.0-1.5 parts of vinyl dimethyl siloxane, γ-aminopropyl triethoxysilane coupling agent 0.5-0.8 parts, 3.5-4.0 parts of paraffin, 25-30 parts of absolute ethanol, 100-110 parts of water, the preparation method comprises the following steps:
[0034] (1) Mix absolute ethanol and water at a mass ratio of 8-9:1, heat to 60-70°C, add γ-aminopropyltriethoxysilane coupling agent under stirring, and stir for 10-15 minu
PUM
Property | Measurement | Unit |
---|---|---|
Length | aaaaa | aaaaa |
Thermal conductivity | aaaaa | aaaaa |
Abstract
Description
Claims
Application Information
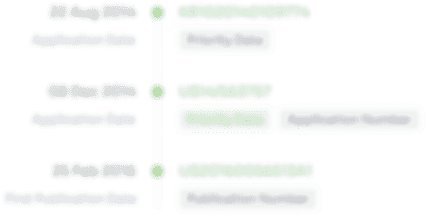
- R&D Engineer
- R&D Manager
- IP Professional
- Industry Leading Data Capabilities
- Powerful AI technology
- Patent DNA Extraction
Browse by: Latest US Patents, China's latest patents, Technical Efficacy Thesaurus, Application Domain, Technology Topic.
© 2024 PatSnap. All rights reserved.Legal|Privacy policy|Modern Slavery Act Transparency Statement|Sitemap