In-situ preparation method of carbon nano-sheet-coated nano-silicon composite material
A carbon nanosheet and composite material technology, applied in electrical components, battery electrodes, circuits, etc., can solve the problems of poor cycle performance, easy explosion, and high cost, and achieve low cost, easy explosion, unsafe, mild conditions. Effect
- Summary
- Abstract
- Description
- Claims
- Application Information
AI Technical Summary
Problems solved by technology
Method used
Image
Examples
Embodiment 1
[0027] S1. Weigh 1.92g, 0.6g and 1.168g of magnesium powder, nano silicon oxide and sodium chloride respectively according to the ratio of the amount of substances of 8:1:2, wherein the particle size of magnesium powder is 70μm, and the particle size of nano silicon oxide The diameter is 40nm, and then the powder is mixed evenly and pressed into a sheet under a pressure of 20MPa by dry pressing;
[0028] S2. Calcinate the sheet material obtained in S1 in a tube furnace under a carbon dioxide atmosphere. During the calcination process, control the flow rate of carbon dioxide to 10mL / min, raise the temperature to 670°C at a rate of 5°C / min and keep it warm for 240min, and the calcination is completed. Post-cooling to obtain the crude nano-silicon coated with carbon nanosheets;
[0029] S3. The carbon nanosheet-coated nano-silicon crude product obtained in S2 is first soaked in a hydrochloric acid solution with a volume fraction of 20% for 30 minutes to carry out a pickling, rem
Embodiment 2
[0031] S1. Weigh magnesium powder, nano-silicon oxide and sodium chloride 0.96g, 0.6g and 0.584g respectively according to the ratio of the amount of substances of 4:1:1, wherein the particle size of magnesium powder is 10μm, and the particle size of nano-silicon oxide is 10μm. The diameter is 80nm, and then the powder is mixed evenly and pressed into a sheet under a pressure of 15MPa by dry pressing;
[0032] S2. Calcinate the sheet material obtained in S1 in a tube furnace under a carbon dioxide atmosphere. During the calcination process, control the flow rate of carbon dioxide to 20mL / min, raise the temperature to 650°C at a rate of 3°C / min and keep it warm for 360min, and the calcination is completed. Post-cooling to obtain the crude nano-silicon coated with carbon nanosheets;
[0033] S3. The carbon nanosheet-coated nano-silicon crude product obtained in S2 is first soaked in a hydrochloric acid solution with a volume fraction of 25% for 60 minutes to carry out a picklin
Embodiment 3
[0035] S1. Weigh magnesium powder, nano-silicon oxide and sodium chloride 2.88g, 0.6g and 4.672g respectively according to the ratio of the amount of substances of 12:1:8, wherein the particle size of the magnesium powder is 10μm, and the particle size of the The diameter is 80nm, and then the powder is mixed evenly and pressed into a sheet under a pressure of 25MPa by dry pressing;
[0036] S2. Calcinate the sheet material obtained in S1 in a tube furnace under a carbon dioxide atmosphere. During the calcination process, control the flow rate of carbon dioxide to 30mL / min, raise the temperature to 720°C at a rate of 5°C / min and keep it warm for 120min, and the calcination is completed. Post-cooling to obtain the crude nano-silicon coated with carbon nanosheets;
[0037] S3. The carbon nanosheet-coated nano-silicon crude product obtained in S2 is first soaked in a hydrochloric acid solution with a volume fraction of 30% for 60 minutes to carry out a pickling, remove the magne
PUM
Property | Measurement | Unit |
---|---|---|
Particle size | aaaaa | aaaaa |
Particle size | aaaaa | aaaaa |
Particle size | aaaaa | aaaaa |
Abstract
Description
Claims
Application Information
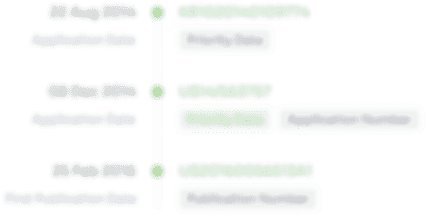
- R&D Engineer
- R&D Manager
- IP Professional
- Industry Leading Data Capabilities
- Powerful AI technology
- Patent DNA Extraction
Browse by: Latest US Patents, China's latest patents, Technical Efficacy Thesaurus, Application Domain, Technology Topic.
© 2024 PatSnap. All rights reserved.Legal|Privacy policy|Modern Slavery Act Transparency Statement|Sitemap